Author |
Message |
Gary Stadler (Boogiethecat) (68.7.217.217)
Rating: N/A Votes: 0 (Vote!) | Posted on Sunday, May 05, 2002 - 2:57 pm: | |
I've heard a lot of folks mention that they've done the McMaster version of spray-on foam insulation and that it's messy but easy, and I've heard a lot of mention about "Grinder / disc / Drywall screws" for flattening the end product, but I'm not getting the whole picture! Can anyone spell it out for me in detail, what the grinding tool looks like and how it's used to get a flat surface? Photos would be super!! Once it's flat, what do y'all cover it with and how? Thanks!! (Next week is foam week for me) Gary |
Jim Stacy (12.87.110.70)
Rating: N/A Votes: 0 (Vote!) | Posted on Sunday, May 05, 2002 - 8:43 pm: | |
Gary, Get a rubber disk made to go in a drill motor and hold a sanding disk or polishing bonnet. I used four 1/4-20 bolts and nuts and installed them in the disk so the thread protrudes about 1 inch from the face that would have the sanding disk attached. Place them evenly so the disk is reasonably balanced. This is a very agressive tool, kind of like trimming your toenails with a chain saw! It will break up the insulation in popcorn size pieces that are too large to be held up by static charge. If you use a grinder or wire brush the particles will float around and stick to everything including your goggles and clothes. Run wires for ceiling fixtures first. It's a good idea to run 12 volt and 120 volt to each roof opening. Then later if you decide to remove a fan and install another roof air, the wires will be there. I chose not to bury any other wires in the walls. I made a chase for the wiring in the back edge of my cupboards so wires can be added or changed. We used 1/2" plywood for wall covering. It provides a non metalic thermal break and a sturdy support for cupboards and partitions. One way. Jim Stacy |
Tom Connolly (64.58.193.211)
Rating: N/A Votes: 0 (Vote!) | Posted on Sunday, May 05, 2002 - 10:56 pm: | |
Gary, I Had a local spray foam insulation company do all the work! The total cost was only $500, they covered the floor and windows with plastic, sprayed the entire coach with hot foam, trimmed the foam flush with the ribs, cleaned up after themselves removed the trimmings with them and did the whole thing in 3 hours in my front yard. After like Jim I installed 1/2 AC on the walls and 1/4 on the radius with a self tapping screws on 4" spacing. I ran all the wiring for the roof Air-Conditioners in advance, I used Contractor grade 12-2 with ground extension cord as it is all fine twisted wire and holds up well with out a lot of cost. The attached picture is the result while it was in progress! Good Luck, Tom
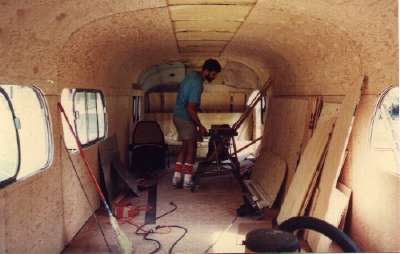 |
mike heron (199.250.136.5)
Rating: N/A Votes: 0 (Vote!) | Posted on Monday, May 06, 2002 - 5:05 pm: | |
Gary: I too am set for foaming this weeekend, up in Spartanburg, SC. Two part cold foam. I had been considering the polishing/buffer wheel type of arrangement for leveling the foam a few days after it cured, with studs in the disc, but the contractor urged me to consider using something different. He recommended tack welding the blade of a 1/2 inch bandsaw to a long straightedge, like the long edge of a Tee that drywall hangers use, then using two people, line this up with the ribs and saw away. I wonder of anyone has done this? It sounds like it might be more precise to the wall cavities, and less messy. Let's keep each other informed about our progress. I am doing an MCI 96a3. My 110 v.wires are buried in the roof and ceiling - all BX. Mike |
FAST FRED (63.215.236.113)
Rating: N/A Votes: 0 (Vote!) | Posted on Tuesday, May 07, 2002 - 5:16 am: | |
I have seen simething close , the fellow attached a Bow wood saw blade to an auto body "Jitterbug" sander and it was real fast . Have also seen a hot wire , usually used to trim foam in either mosel or Experimental air craft , stretched on a wooden bow that fit over 2 ribs . This smelled , but was fast and much neater than sawing , or grinding. FAST FRED |
OAE Palmer (208.164.96.18)
Rating: N/A Votes: 0 (Vote!) | Posted on Tuesday, May 07, 2002 - 6:41 am: | |
I saw this topic when it first popped up, but was tite for time and didn't reply. The "hot wire" set-up Fred mentioned is available anywhere that sells foam in qty....I have seen them sell for $30-$90 and they work so fast with so little clean-up afterward I am suprised it is not SOP for every foam operation! You can make one from the Ni-Chrome wire inside a toaster, 2 insulators and "slingshot" handle. Basicly what you are making is a large cheese slicer, and electrifying the wire. I have also seen an air powered hacksaw (open ended) using a thin Japanese wood saw blade about 20inches long X 1 1/2 in.high, looks simular to a electric carving knife. BTW & FWIW, if you "skin" the foam with mylar space blanket material (any walmart 2bux) after you are done leveling out the foam....it will be like adding another inch of foam and will only take you another hour and some box tape! |
Gary Stadler (Boogiethecat) (68.7.217.217)
Rating: N/A Votes: 0 (Vote!) | Posted on Tuesday, May 07, 2002 - 8:04 am: | |
Hmmm, great idea the hot-wire!! A suggestion if you want to make one though... go to an appliance repair place and get a "dryer restringing kit" which will be a very heavy nichrome wire. Toaster wires are very delicate and might not be able to take the stresses you'll give em while cutting foam. Now, the restringing kit wire will be a certain length when you stretch it out, and it will want to operate on 220 at a few thousand watts. Way too much. The whole length might be ok on 110 but it would be better to be able to control the much shorter length you'll end up with. You'd need either a variac (variable auto-transformer- on ebay all the time) that can handle 10 amps or a step down transformer and a smaller variac to make that 3-4ft piece of that nichrome wire that you'll end up with work at the correct temperature. I'm gonna try this so I'll write up the specifics in a few days. It sounds MUCH more appealing than ground up foam dust everywhere!! Also remember that the hot wire, when finished, will be hooked directly to the power line unless you use an isolating step-down transformer (way too much hassle)... fortunately the bus is probably on rubber tires so zapping on the metal frame won't be too much of a problem, but you still could get shocked if not careful... |
R.C. Bishop (128.123.88.50)
Rating: N/A Votes: 0 (Vote!) | Posted on Tuesday, May 07, 2002 - 10:04 pm: | |
Am just guessing that the mylar would work whether spray foamed or block??? Comments? Thanx, RCB |
Tom Caffrey (Pvcces) (12.146.33.84)
Rating: N/A Votes: 0 (Vote!) | Posted on Tuesday, May 07, 2002 - 11:11 pm: | |
Hey Gary, Why not just use a short length of the wire and hook it to a 12 volt battery? With some experimenting, it shouldn't be too hard to find a length that the 12 volt battery will heat just right. If it turns out that the wire will be too short to be useful, then hook two 12 volt batteries in series. Something like that has to be easier than hooking up to 110. Once you figure it out, I would think one full charge would be enough to get the job done. For what it's worth. Tom Caffrey PD4106-2576 |
Gary Stadler (Boogiethecat) (68.7.217.217)
Rating: N/A Votes: 0 (Vote!) | Posted on Tuesday, May 07, 2002 - 11:58 pm: | |
Heya Tom! Good idea, it would certainly work. I've used hot wires before though, and most of the time it's way easier to have the length fixed, so having that variac and just dialing it to the right temperature is much easier than fiddling with wire length/gauge. But the battery thing would work well if you got the length right and it was a workable length. I'm certainly gonna try this first on my foaming job! Thanks!!! Gary |
OAE Palmer (208.164.96.38)
Rating: N/A Votes: 0 (Vote!) | Posted on Wednesday, May 08, 2002 - 2:57 am: | |
The mylar would be best used if used between the foam and the outer metal skin of the coach, however that renders the surface too slick for the foam to adhere correctly. So the inside of the foam is about your only alternative, however give this some thought... the stripped out interior of my 4106 has mylar over most of the interior overhead ribs, last week I did another test on the ambiant temp 2 inches from the rib surface. The exterior air temp was 91 the interior temp 2 in. away from the mylar surface was 109..... 2 in. away from bare roof w/o any insulation was 125. That is a significant variation for only 1 mil of protection, especially when you consider the time and labor involved (1 hour and $20.) verses the constant savings in propane and uncomfortability. I was first educated on reflective mylar by a news story about a man in Bemidji MN who built a house that only used 50 gallons of fuel oil a winter, about 1/10th that of the norm! His trick was mylar on both sides of 6 inches of foam, he claimed they pretty much heated the house with body warmth and the normal heat from lights and the coffee maker! I like to imitate smart people, and he was one! |
DaveD (216.18.113.69)
Rating: N/A Votes: 0 (Vote!) | Posted on Wednesday, May 08, 2002 - 1:58 pm: | |
I'd use nichrome wire and a lower voltage source through an isolating transformer, 42V or less. This will limit the length of nichrome wire you can use, but the risk of handling an uninsulated wire connected directly to 110V is not worth it. 60mA current can stop a heart, not to mention the potential for burns or other damage, even if you do survive. DaveD |
|