Author |
Message |
Glenn Williams (Glenn)
Registered Member Username: Glenn
Post Number: 138 Registered: 6-2006 Posted From: 216.163.57.205
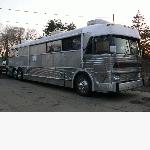
Rating: N/A Votes: 0 (Vote!) | Posted on Thursday, March 06, 2008 - 9:51 pm: | |
After looking at Mark Renner's beautiful electric radiator fans, I got to wondering. I know, bad idea! Has anyone used or figured out if it is possible to use the original heat motor or condenser motor to power the original squirrel cage fans? I think everything needed is in the heat electrical system - relays, etc. Any thoughts? |
Luvrbus (Luvrbus)
Registered Member Username: Luvrbus
Post Number: 309 Registered: 8-2006 Posted From: 74.33.43.159
Rating: N/A Votes: 0 (Vote!) | Posted on Thursday, March 06, 2008 - 9:56 pm: | |
Glenn,I seen it on a MCI5 the guy said it worked great but I don't know if worked or not he was at the last rally at the caverns and it was a nice bus (Message edited by luvrbus on March 06, 2008) |
Mark Renner (Boomer)
Registered Member Username: Boomer
Post Number: 85 Registered: 11-2006 Posted From: 12.180.53.193
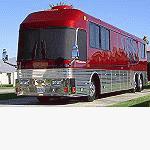
Rating: N/A Votes: 0 (Vote!) | Posted on Friday, March 07, 2008 - 12:44 am: | |
It would be very difficult (but not impossible, with enough time and money) to use either your condenser or evaporator motors, as nice as it would be if you are tossing them anyway. Here is why: On an MC-9, for instance, they used an Ohio motor for the condenser, 24V, 2 hp, 2200 rpm, drawing a whopping 52-71 amps. The evaporator motors are nearly as big; 1.5 hp, 2900 rpm and drawing 53-70 amps. You would probably have to retain your 50DN alternator to power those bad boys. Also, if your idea is to drive the miter box with a single motor you would have to turn it around with the input facing forward, then you would have to reverse sides with the squirrel cage fans. Lastly, there is not room in the fan compartment for both the gear box and electric motor. I guess you could extend the compartment forward, but thats a lot of work. Then you would still have the horsepower loss and maintenance associated with the miter box. The only thing you would have gained is doing away with the belt and belt tensioner. There is a lot simpler way to do this: Get rid of the miter box and squirrel cage assemblies altogether and simply mount two 24V electric fans in the compartment. The 24V Prevost condenser fan motors would be a good conversion, as the fans would be about the right size. The later model H3 Prevosts used the LeRoy-Somer motors, rated at .57 hp, 1950 rpm, and draw only 23 amps! Fabricate your fan motor mounts, and shrouds, install your wiring, and it's all a pretty straight forward conversion. If I had a MC7-8-9, that's how I would do it. |
Glenn Williams (Glenn)
Registered Member Username: Glenn
Post Number: 140 Registered: 6-2006 Posted From: 216.163.57.205
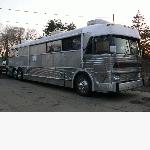
Rating: N/A Votes: 0 (Vote!) | Posted on Friday, March 07, 2008 - 7:45 am: | |
Great thoughts Mark! I do plan to keep the 50DN alternator to power my Xantrex 4024 while going down the road to supply air conditioning. I had not thought about using an electric motor to drive the gearbox. That would be difficult and a real pain! I was imagining just pulling the gearbox and putting in the heater blower motor. |
Glenn Williams (Glenn)
Registered Member Username: Glenn
Post Number: 141 Registered: 6-2006 Posted From: 216.163.57.205
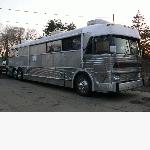
Rating: N/A Votes: 0 (Vote!) | Posted on Friday, March 07, 2008 - 10:22 am: | |
OK, I read some of the nastiness that happened here in 05 and I think I'll just leave well enough alone! Ian, thanks for keeping archives! There is a lot to learn from other's mistakes! |
Luvrbus (Luvrbus)
Registered Member Username: Luvrbus
Post Number: 310 Registered: 8-2006 Posted From: 74.33.43.159
Rating: N/A Votes: 0 (Vote!) | Posted on Friday, March 07, 2008 - 11:06 am: | |
Glenn think that was bad you should have been around on the old MAK board it had some that made that one look civil but you can find anything that was ever posted here( Ian is like Vegas) |
George M. Todd (George_mc6)
Registered Member Username: George_mc6
Post Number: 373 Registered: 8-2006 Posted From: 207.231.75.253
Rating: N/A Votes: 0 (Vote!) | Posted on Friday, March 07, 2008 - 1:06 pm: | |
Mark, I really like your bus, there is obviously a LOT of work that has been put into it! (And that is just looking at the outside pictures.) That said, I am a heating and air conditioning contractor, which means I SHOULD understand air and water flow, and heat transfer. I also understand fan horsepower requirements, and it is very frustrating to look at the majority of busses that have continuously driven radiator fans, and the large amount of wasted horsepower, and fuel, that this practice causes. The bus companies put shutters across the radiators in an effort to save fuel by running the fan(s) in thinner air when the engine doesn't need cooling, but it is still a drag. Anyhow, my bus is one of a hundred MCI oddballs that has one large slab radiator, and a hydraulic fan motor, which is thermostatically controlled, and doesn't run at all when cooling is not needed. It cools the 12V71 well, the only time the alarm came on was climbing the Baker grade out of Las Vegas, at 75 mph, and 105 degrees. I am familiar with another one of these with an 8V92T and a 740, and it has no problem cooling either, which leads me to ask you these questions. One, I understand that my 6 blade, 28 inch diameter radiator fan draws between 20 and 25 horsepower at 2100 rpm, so I wonder how you are able to accomplish this with only 1.14 horsepower? Two, have you driven your bus uphill on a 100 degree day at full throttle for several miles without it overheating yet? You mention maintaining mitre boxes, but you don't mention putting brushes in DC motors? I'm really not trying to give you a bad time, I'm just curious, because no experience has been posted yet!!! George |
Luvrbus (Luvrbus)
Registered Member Username: Luvrbus
Post Number: 311 Registered: 8-2006 Posted From: 74.33.43.159
Rating: N/A Votes: 0 (Vote!) | Posted on Friday, March 07, 2008 - 1:37 pm: | |
does the MCI D4505 and the Prevost H3 45 use 3 speed electric fans for engine cooling |
Skip N (Skip)
Registered Member Username: Skip
Post Number: 19 Registered: 11-2006 Posted From: 161.7.2.160
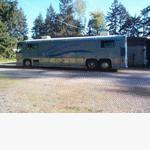
Rating: N/A Votes: 0 (Vote!) | Posted on Friday, March 07, 2008 - 2:04 pm: | |
Still trying to understand all of this which leaves me with the question: At 2100rpm what are the SCFM of each type(squirrel cage and 6 blade 28"diam.)? Or does that matter? Thanks in advance Skip |
Mark Renner (Boomer)
Registered Member Username: Boomer
Post Number: 87 Registered: 11-2006 Posted From: 12.180.53.193
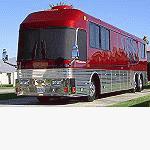
Rating: N/A Votes: 0 (Vote!) | Posted on Friday, March 07, 2008 - 4:32 pm: | |
George, in referance to your very good questions, I'm afraid that my answers (to the degree that I can fully answer them), involves a little history in this project, and will be lengthy, but here goes: I first became interested in converting to electric as I was starting my conversion. At that time I owned a fleet of new Prevost H3's and a half dozen MC-9's. I admired the way Prevost engineered their condenser fan setup, and believed it could be carried over the radiator. Prevost tech support could not give me exact heat transfer data, but suffice it to say, it is substantial. Attached is a picture of their application. Next, I went to Flexalite Fan Co. to speak with thier engineers. They offered no products that would do the job, however the discussion was somewhat helpful. At that time, I was certain that whatever I designed would fall in the catagory of "experimental", with the outcome to be determined with a lot of testing. My motors are built by Scott Electric. 40 amp, permanant magnet, 1/2 hp, 1,600 rpm. I wanted to copy the Prevost setup as nearly as possible, so spec'd a 5/8 shaft so the Prevost fan blade assemblies could be used. The shroud was built to achieve about 1/8" clearance, and the blades are set at nuetral depth in the shroud (half way in). At that time, I had a nearly new 6V92TA with 9F80 injectors and a mini by pass blower which I estimate was putting out around 370 hp. The cooling requirements for this, as you can guess, would be substantial. The first test run (empty shell weighing about 25,000 lbs. was on a 90 degree day and up a grade of about 5% for about 5 miles. At the top, only fan #1 was on, and maintaining 190 deg. under a full power ascent, which took a load off my mind. Let me pause right here to say that I built this system for more reasons than to beat the parasitic hp loss. The Eagle Model 10 set up drives straight off the crankshaft, through a flex coupling and into the gearbox, with a driveshaft then going both left and right to the A/C compressor on the right, and on the left making a transition to pullys, pillow blocks, idlers, etc. until it gets to the fan hub. Removing all this junk saved a TON of weight and complexity. I should have weighed it all, would like to know how much. After concluding all this work, I found a nearly new Cummins ISM with World transmission (test engine with only 26 total hours), so I removed the 6V and installed the new power pack. I am controlling the fan motors individually, with fan 1 coming on at 195 deg coolant temp, and fan 2 coming on at 200. In addition, I installed an intake air temp switch to activate both fans at 160 deg of intake air temp. (the ISM will throw a code and begin ramp down at 190 deg. intake air temp). I also have switches on the dash to manually active both fans in the event of a switch failure downstream, and fan on indicator lights. The wiring passes through two common 12v starter type relays. To date I have accrued about 6,000 miles with this set up, with about 1,000 with the 6V92. I have not yet made my closing pieces around the outside of the radiator/charge air cooler (stacked). There is massive air flow leakage around a gap which is about 2". I have left this for last because I intend to have a new high performance radiator built this summer to replace the 27 year old, inefficient stock unit. Now to the grist of your question. Have I operated it up the Baker grade at 100 plus? No sir, I have not. Yet. Been over the Siskyous, Donnor, and S. Oregon mountains though. Is this the final, best answer? Remains to be seen. It's still a test in progress, but I am happy with it so far, and that's all that counts. As an aside, the cost was reasonable too. I have about $1,000 in parts in this; motors,fans, stainless shroud fabrication, relays, switches, wiring, etc. Your observation about the hp requirements of your set up, I believe, is correct. My goal was to have NOTHING turning when the fans are off, saving hp, and also to lose a lot of weight, complexity, and maintenance. I realize that this may be a nebulous answer, and am more that happy to answer any more questions you might have. By the way, for those who wonder why the manufacturers never used electric (some do now), the venerable Delco 50DN generator in it's various ratings of from 250 to 300 amps, were pretty much maxed out with the normal bus electrical loads, plus huge condenser and evaporator motor requirements. I am no expert in this field at all. Would like to build a better mouse trap tho. To each his own!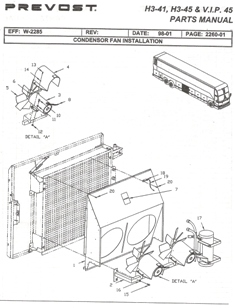 |
George M. Todd (George_mc6)
Registered Member Username: George_mc6
Post Number: 374 Registered: 8-2006 Posted From: 207.231.75.253
Rating: N/A Votes: 0 (Vote!) | Posted on Friday, March 07, 2008 - 6:07 pm: | |
Skip, In my opinion, it matters a WHOLE lot! I don't have a clue as to how much air these things move, but I'm sure that somebody will have either a formula, or some published figures. In my case, I don't know whether my pump displacement and my hydraulic motor's oil requirement per revolution are the same or not. My pump is driven by the auxiliary drive, at engine speed, and if the pump puts out more oil per turn than the motor consumes, the fan would turn faster than the engine. Likewise, if the motor needs more oil per turn than the pump produces, the fan will run slower. I am a firm believer in not running fans when you don't need them, especially in light of the present oil prices! Several things to consider: There is no free lunch, all fans take horsewpower to run them, whether it comes from the engine via shafts, mitre boxes, and belts, or via a hydraulic pump driven by the engine, or via wires from the alternator driven by the engine. Each of these systems has a very small amount of loss in transmitting the power from the engine to the fan, the GREAT loss is in running the fan when it is not necessary! Shutters do help, as the fan(s)are running in thinner air when the shutters are closed, so they waste less power, but they are still wasting a lot of power. Electrics consume nothing, neither do hydraulics with the bypass valve open, or clutch fans with the clutch de-energized. This whole thread is about airflow, I'm just having problems believing that a 450-500hp engine with a rear-mounted sideways radiator can be cooled with ONE horsepower worth of fans! All of the newer trucks have a clutch fan in the interest of fuel economy, but remember that their radiators face forward, over about 40 mph, they don't need a fan at all. Unfortunately, we're not so lucky. One little number to throw out, 746 watts per horsepower, @ 100% efficiency. So, by Mark's ratings, either his 1/2 hp motors are really inefficient, or they're actually closer to 3/4 hp each. I don't feel that an extra 1/2 hp would make a difference, either. The bus in question MAY run 62 mph on the flat in November as equipped, without overheating. But I will make a LARGE WAGER that it won't go up a grade in August at a hundred outside, at 30-50 mph in full throttle, period. (Remeber he says he has electronics, so they will shut it down when it gets too hot.) Charge air cooling isn't mentioned either, that engine has it, (remember the comment about the fans coming on at 160 inlet air temp?) That sounds to me like the aftercooler is in front of the radiator, but what do I know, I'm an MCI owner with a Detroit that has air to water charge cooling. The end result is about the same, the load is still on the radiator, it just gets there differently, and I'm being a wiseacre. Maybe a question is in order here.... If one of the major bus makers could cool their bus with a 10th to a 20th of the parasitic load of the competition, and the resulting power and fuel economy increase, wouldn't they do it? I also did exactly what Mark has done, only with a gas 440 to a 6BT Cummins in a 75 3/4 ton pickup that got a used utility bed off a Chevy at the same time. Astounding results with one electric fan in front of the radiator, as no room for the belt driven fan behind, or the A/C condenser in front of it either. So the cond. went on the left side where the fuel tank would have been on the Chev, (Dodge puts the tank inside the frame) and is cooled by another elect. fan and a custom shroud. The engine never gets hot, because the radiator was designed for a lot more heat out of the gas engine, and the warmer inlet air from the A/C condenser, and the A/C works better at idle than it did before, because it is always getting lots of airflow. FWIW, Gerge |
john w. roan (Chessie4905)
Registered Member Username: Chessie4905
Post Number: 913 Registered: 10-2003 Posted From: 71.58.48.5
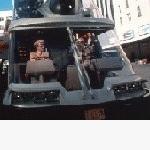
Rating: N/A Votes: 0 (Vote!) | Posted on Friday, March 07, 2008 - 6:38 pm: | |
At least he is getting closer as to what is needed to have a serious electric fan cooling setup. Take a look at a city bus with electric cooling fan,s to cool the AC condenser. I dismantled a Flxible a couple of years ago that had one and that motor was pretty large with a bout a 30 inch multiblade. Probably drew over 100 amps when running. For a comparable coach radiator size you'd need two or, in case of the giant radiators on some of the newer Eagles maybe three. That much amperage draw will probably equal the drag on the engine that a normal fan will create. The major benefit I see in savings, is the ability to only have as many of the fans operating as needed due the particular driving conditions encountered at the time. Electric, hydraulic, variable speed etc. are all going to need to move the same amount of air and, I suspect draw the same amount of horsepower draw, whether through the alternator or directly from the engine. You can set it up to draw a lot of current from the batteries going up the big grades and then charge it back on the level and down grades, but how complex is that going to get and how much benefit? The simplification and weight cutting and space saving issues are another thing. I think TWO DOGS just didn't understand that those dinky fans COULDN'T move the air necessary to adequately cool that engine. Compare the pitch and width of a coach fan blade. What is it- 4 to 5 inches? Those auto electric fans are probable an inch at best. Think of that pitch like screw threads. The wider the pitch, the more air that is going to pass at the same given speed. Of course blade numbers and diameter also matter. Some of the new computer designed fan blades that some of these companies produce now for OTR trucks may be a real benefit to some of us with cooling issues. I saw that one of the companies offer multiblade reverse rotation blades with universal mounting that might work well on some of our GM coaches with cooling issues. I wonder if anyone has tried any of them. Sorry for rambling on. It's Friday and my fingers are de stressing from the past week. |
George M. Todd (George_mc6)
Registered Member Username: George_mc6
Post Number: 376 Registered: 8-2006 Posted From: 207.231.75.253
Rating: N/A Votes: 0 (Vote!) | Posted on Friday, March 07, 2008 - 11:46 pm: | |
Mark and John, I really appreciate all the answers and the positive discussion! To me, it doesn't matter whether its Baker or Donner. If it will go up Donner or the Siskyous on a warm day, it will go anywhere. We definitely all agree that we need to get rid of continuous running mechanically driven radiator fans, or pay the consequences. Regards, George |
doug yes (Dougg)
Registered Member Username: Dougg
Post Number: 43 Registered: 1-2007 Posted From: 71.29.24.90
Rating: N/A Votes: 0 (Vote!) | Posted on Saturday, March 08, 2008 - 8:36 pm: | |
Why electric fans are not on new busses? Most likely because of the huge AC system. I drove a tour up the Grapevine last summer.(MCI 102 DL3 with a Series 60 and new radiator and fans) I tried to load everyone up early to beat as much heat as possible but still I had to turn of the coach AC to keep from overheating. Opening the roof hatches kept eveyone sweaty but alive. |
|