Author |
Message |
Roger Baughman (Roger)
Registered Member Username: Roger
Post Number: 91 Registered: 11-2006 Posted From: 69.232.64.102
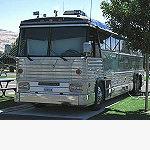
Rating: N/A Votes: 0 (Vote!) | Posted on Friday, April 03, 2009 - 3:27 am: | |
I am going to remove the orginal bus air and use the batteries/inverter to power the two roof air's, for on the road use. Now I want to install a car/truck air for the driver's area. Sean said not to use a compressor at the engine as it is too far, (40ft) to work good. OK, what about powering the compressor with a AC motor in the old condenssor compartment (MCI9) foward of the first bay drivers side. All ideas welcomed. Roger |
FAST FRED (Fast_fred)
Registered Member Username: Fast_fred
Post Number: 740 Registered: 10-2006 Posted From: 66.82.9.23
Rating: N/A Votes: 0 (Vote!) | Posted on Friday, April 03, 2009 - 6:46 am: | |
"Now I want to install a car/truck air for the driver's area. Sean said not to use a compressor at the engine as it is too far, (40ft) to work good." There is a shop near Atlanta that would be really supprised to learn the hundreds they installed don't work. Go Figure , their customers never told them of their decades of failure!! FF |
Nick Badame Refrigeration Co. (Dnick85)
Registered Member Username: Dnick85
Post Number: 282 Registered: 2-2006 Posted From: 75.198.246.205
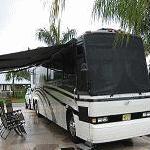
Rating: N/A Votes: 0 (Vote!) | Posted on Friday, April 03, 2009 - 6:54 am: | |
Hi Rodger, The 40' distance between the engine compressor and your dash system is a minor btu loss compaired to btu capacity you will gain. The avarage dash system is 52,000 btu's. Thats about 4 1/2 tons of A/C and you might loose 5 - 7 thousand btu's on the line set travel. To me, the dash system would have far less running components then your roof a/c's operated by your inverter and battery bank [as well as having less capacity with your max 2-15,000 btu roof airs]. Good Luck Nick- |
Luvrbus (Luvrbus)
Registered Member Username: Luvrbus
Post Number: 683 Registered: 8-2006 Posted From: 74.32.92.133
Rating: N/A Votes: 0 (Vote!) | Posted on Friday, April 03, 2009 - 9:06 am: | |
Rodger,1000's of buses use the engine mounted compressors for dash air.I have had one for 15 years with no problems.www.rdac.com |
Roger Baughman (Roger)
Registered Member Username: Roger
Post Number: 92 Registered: 11-2006 Posted From: 69.232.64.102
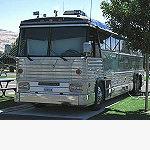
Rating: N/A Votes: 0 (Vote!) | Posted on Friday, April 03, 2009 - 10:10 am: | |
Nick, I am going to install both systems, the dash air and the roof air's running of of the batteries. I need both to assure comfort. I have run the roof air's off of my generator, and it is not quite enough for the driver too. It gets very hot here in California. The redundancy is for back up and lower operating cost. |
Nick Badame Refrigeration Co. (Dnick85)
Registered Member Username: Dnick85
Post Number: 283 Registered: 2-2006 Posted From: 76.124.92.192
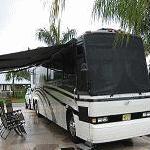
Rating: N/A Votes: 0 (Vote!) | Posted on Friday, April 03, 2009 - 10:47 am: | |
Hi Rodger, I would say, purchace the larger 6 ton system for your dash and use the fans in your roof airs just to circulate the cool air from the dash system, to the rear of the coach. Or, you can just keep your main OTR heat blower to circulate the cool air to the rear. Either way, it would keep you from trying to invert power for the big load.. Besides, it's no fun when both roof air's try and start at the same time and end up blowing the 400amp Jllg fuses on your battery bank... Especially when your are rolling down the road! BTDT Nick- |
Sean Welsh (Sean)
Registered Member Username: Sean
Post Number: 813 Registered: 1-2003 Posted From: 67.142.130.18
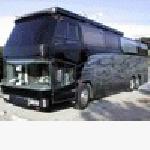
Rating:  Votes: 1 (Vote!) | Posted on Friday, April 03, 2009 - 1:08 pm: | |
Just to clarify what I said to Roger: I wrote
quote:We ripped the engine-driven driver air out of our bus -- too many problems. 40' is a long way to pump refrigerant for such a small compressor. We went all-electric instead.
I did not say that it wouldn't work. The folks who did ours (the original converter, I imagine) did not do their homework, and both compressors seized. Like anything else, it requires careful system design and appropriately sized components. You can't just throw in some compressor you got cheap at AutoZone or off eBay, string 100' of hose, and expect it to work with an existing dash evaporator that was intended to be run from a giant bus system. -Sean http://OurOdyssey.BlogSpot.com |
George M. Todd (George_mc6)
Registered Member Username: George_mc6
Post Number: 770 Registered: 8-2006 Posted From: 64.55.111.6
Rating: N/A Votes: 0 (Vote!) | Posted on Friday, April 03, 2009 - 3:13 pm: | |
Sean, As usual, you've got my vote! If you've read my off bd e, you have seen my concerns. We discussed compressor sizing and oil return problems before I left. The main cause of belt driven compressor failures IS lack of lube, followed by operation at too high head pressure. Liquid slugs enter the picture also. All are preventable by design... By "...both compressors siezed.", I assume you had one that siezed and was replaced with another that failed? All the oil laying in the front of the system, and/or all of it coming back at once while going uphill would be really hard on a comp! (I think thats what they make traps and accumulators for?) Lotsa regards, G |
Sean Welsh (Sean)
Registered Member Username: Sean
Post Number: 814 Registered: 1-2003 Posted From: 67.142.130.18
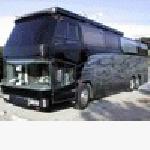
Rating: N/A Votes: 0 (Vote!) | Posted on Friday, April 03, 2009 - 4:11 pm: | |
George, We had two compressors (and four condensers with electric fans, and, I recall, two evaporators). We could never get the specs for the dash evaporator when we went to re-do the system. The whole unit (including blower and heater coils) was pretty old and cantankerous anyway, so we replaced it with a Red Dot. Rather than run new lines all the way back to the engine, re-do the compressors, and fix up the condensers, we put a new Red-Dot condenser behind the front grille, where it gets ram air when we are under way (with a Red Dot 24-volt fan to supplement as needed and when stopped, although it screams like a banshee), then coupled it all up to a 120-volt Copeland refrigeration compressor. I discussed this system way back here: http://www.busnut.com/bbs/messages/233/19627.html#POST122604 It should be noted that HVAC is not my forté, and I had a refrigeration professional size the compressor and condenser based on the evaporator we selected, and charge the system. But my hoses are only a couple feet long, and I can run the system while parked on shore (or generator) power, which is helpful in really hot conditions because my driver area is downstairs, where the roof airs can't cool it. -Sean http://OurOdyssey.BlogSpot.com |
George M. Todd (George_mc6)
Registered Member Username: George_mc6
Post Number: 772 Registered: 8-2006 Posted From: 64.55.111.6
Rating: N/A Votes: 0 (Vote!) | Posted on Friday, April 03, 2009 - 4:31 pm: | |
Sean, Thanks for the info. I don't feel that your original system as described could last. Oil is just going to stop where there is low Freon flow in an uphill pipe, and stay there, period. In a parallel system, thats going to be the lowest condenser, the lowest evap, etc. I really like your comments on "refrigeration professional sizing" as this is something that just can't be done DIY. (I appreciate the "wisdom" too!) Thanks AGAIN, George |
Roger Baughman (Roger)
Registered Member Username: Roger
Post Number: 93 Registered: 11-2006 Posted From: 75.3.205.82
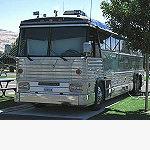
Rating: N/A Votes: 0 (Vote!) | Posted on Friday, April 03, 2009 - 7:40 pm: | |
Sean, Thanks for your help. I didn't mean to step on any toes. I am just trying to learn from you guy's, so I don't make some dum expensive mistakes. Roger |
Wec4104 (Wec4104)
Registered Member Username: Wec4104
Post Number: 23 Registered: 7-2008 Posted From: 68.80.242.72
Rating: N/A Votes: 0 (Vote!) | Posted on Saturday, April 04, 2009 - 8:13 am: | |
Reading through this thread, I got to thinking (theoretically), about a compressor mounted in the engine compartment with a dual belt system. Using automotive type belt clutches, it would be set up to run in either of two modes: In the first mode, it is driven off the bus engine like a typical automotive style A/C unit. In the the second mode, you throw a switch and the belt clutch connects it to a decent size 110 VAC electrical motor. You could use this mode with shore power, or with your generator when boondocking or while rolling down the highway when you needed the bus' full horsepower. I'll admit I haven't looked at the sizing requirements for the electrical motor or the amp draw. But I can see a number of nice advantages to this type of system. Any thoughts, or anyone ever heard of anybody with such a system? |
Luvrbus (Luvrbus)
Registered Member Username: Luvrbus
Post Number: 684 Registered: 8-2006 Posted From: 74.32.92.133
Rating: N/A Votes: 0 (Vote!) | Posted on Saturday, April 04, 2009 - 8:38 am: | |
Wec, Pro Air and Fridgett makes those type units.I don't know how they work but I have seen them fwiw |
Wec4104 (Wec4104)
Registered Member Username: Wec4104
Post Number: 24 Registered: 7-2008 Posted From: 68.80.242.72
Rating: N/A Votes: 0 (Vote!) | Posted on Saturday, April 04, 2009 - 9:07 am: | |
Thanks, Luvrbus. I tried a couple of quick internet searches to see if I could find anything on those units. "Pro Air" is such a common term, it yields thousands of dead ends. I put "Fridgett" and "air conditioner" together into a single Google search, and it came up completely empty. Hmmm. I was curious to see if I could find specs for the BTU rating, motor amp draw, SEER, etc. |
Luvrbus (Luvrbus)
Registered Member Username: Luvrbus
Post Number: 685 Registered: 8-2006 Posted From: 74.32.92.133
Rating: N/A Votes: 0 (Vote!) | Posted on Saturday, April 04, 2009 - 9:20 am: | |
wec,try www.danhard.com and ambulance air conditioning companies.I don't think the automotive type use a seer rating (Message edited by luvrbus on April 04, 2009) (Message edited by luvrbus on April 04, 2009) |
Nick Badame Refrigeration Co. (Dnick85)
Registered Member Username: Dnick85
Post Number: 284 Registered: 2-2006 Posted From: 75.199.43.221
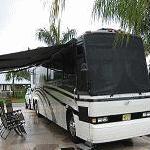
Rating:  Votes: 1 (Vote!) | Posted on Saturday, April 04, 2009 - 4:15 pm: | |
Hi Wayne and Clifford, Unfortuinatly, you would need about a 5 to 8 hp electric motor to turn the compressor. I will have to do the numbers to give you the correct sizing. Secondly, you would have to remember that the condencer fans also need to be running. It might turn out to be an expensive way to cool your coach on land power. Nick- |
Wec4104 (Wec4104)
Registered Member Username: Wec4104
Post Number: 25 Registered: 7-2008 Posted From: 68.80.242.72
Rating: N/A Votes: 0 (Vote!) | Posted on Saturday, April 04, 2009 - 8:47 pm: | |
The size of the electric motor was one concern I had. On the other hand, it would have the cooling power of 3+ roof top units. If the motor would need to be 240 volt to run efficiently, I think that might be enough to kill the idea of a dual mode system. Fun to explore these ideas, however. |
George M. Todd (George_mc6)
Registered Member Username: George_mc6
Post Number: 773 Registered: 8-2006 Posted From: 64.55.111.6
Rating: N/A Votes: 0 (Vote!) | Posted on Sunday, April 05, 2009 - 7:07 pm: | |
1. Nick is right, and he's got my vote. We're both air conditioning contractors, for what that's worth... 2. Most hiway buses have 7-12 Tons of capacity, with a ton being 12,000 BTU. So, a 13,500 BTU roof air with a 10 EER efficiency rating will consume 1,350 Watts at 85 degrees outdoor. More as the outdoor (ambient) temp rises. It takes 746 Watts to produce 1 Horsepower, theoretical perfect, so two horsepower would take 1492 Watts, which all can see is just a hair more than the draw of one fairly efficient roof air. Then, 6 horsepower, which is only the compressor requirement, would take 37.3 amps at 120 Volts, under 85f, with perfect power. Add in the condenser and evaporator fans at 5 amps each, and 47.3+ amps is a whole lot of 120 Volt juice. 5hp is the largest off the shelf single phase 240 V motor available, 7 1/2 horse can be ordered. I don't exactly understand the clutch idea either, but I think it is a moot point! Interestingly enough, the full load amperage on a 240 Volt Copeland ZR36K3 compressor is 19 Amps. FLA is usually about 10% over actual current draw, and this comp will produce about 40,000 BTU with the right coil and condenser sizing, expansion valve, etc. Still gotta have cond and evap fans.. The heat load on a bus with factory ducting supplying air under windows thru thin walls, (with thin insulation!) is going to be way over 3+ tons, while 3 roof airs will do the job. A whole lot of thought is going into this subject off board right now, so lets see how it shakes out! (Just designing some dependable practical automatic switching controls, etc., that will fit in an existing panel.) Regards, George |
Wec4104 (Wec4104)
Registered Member Username: Wec4104
Post Number: 26 Registered: 7-2008 Posted From: 68.80.242.72
Rating: N/A Votes: 0 (Vote!) | Posted on Sunday, April 05, 2009 - 9:44 pm: | |
In a nutshell, I was wondering about the feasibility of a single high output AC system (4+ ton) that could run off of the bus engine or electric. Running it off the bus engine seems pretty straightforward, as automotive type systems over 5 tons are rather common place. The compressors are generally belt driven and there is an electrically activated clutch pulley. When the unit is turned off, the clutch pulley "free wheels" such that the belt spins the pulley, but it is not engaged with anything. When activated, the pulley engages witht he shaft causing active rotation of the compressor shaft. I pictured a compressor with an extra long shaft and yet another clutch pulley on it. This pulley would have a belt connecting it to an electrical motor. The air conditioner controls would allow three modes: Off (both pullies free wheeling), Engine Driven (engine clutch engaged, motor free wheeling), Electric powered (engine pulley free wheeling, electric motor pully engaged). The question was posed as a feasibility thing, not having run the numbers to determine motor requirements. If it would be possible, I see lots of advantages. |
Wec4104 (Wec4104)
Registered Member Username: Wec4104
Post Number: 27 Registered: 7-2008 Posted From: 68.80.242.72
Rating: N/A Votes: 0 (Vote!) | Posted on Sunday, April 05, 2009 - 10:18 pm: | |
Sorry, but as I kick this around in my head, I have another question (Nick or George) which will undoubtably show my lack of understanding for these A/C systems. But here goes: Suppose you have a conventional style automotive air conditioning system that is rated at 5 tons (60K BTUs). It is belt driven off of the engine, with the pulley diameters selected so that the compressor has full output in the engine's normal power range. Now let's say you wanted to wanted to drive this same compressor with an electrical motor. However, you were willing to give up some cooling to use a smaller motor. If the pulley sizes were selected to run the compressor at 2/3 speed could you use a less powerful motor and simply give up some of the cooling output? Going back to my dual clutch belt drive idea, could the shaft have two different pulley diameters? On the highway, when you need the most cooling, the compressor spins more quickly and gives you 5 tons of cooling. When parked, the smaller electrical motor spins the compressor at a reduced speed so you have a rated output of only 3 tons. Does any of this make sense? |
Tom Caffrey (Pvcces)
Registered Member Username: Pvcces
Post Number: 1275 Registered: 5-2001 Posted From: 65.74.69.200
Rating: N/A Votes: 0 (Vote!) | Posted on Sunday, April 05, 2009 - 10:27 pm: | |
I don't see why you would need the clutch on the AC motor. Couldn't it just be allowed to spin when the AC is engine driven? Just curious. Tom Caffrey PD4106-2576 Suncatcher Ketchikan, Alaska |
FAST FRED (Fast_fred)
Registered Member Username: Fast_fred
Post Number: 744 Registered: 10-2006 Posted From: 69.19.14.40
Rating: N/A Votes: 0 (Vote!) | Posted on Monday, April 06, 2009 - 6:02 am: | |
"Suppose you have a conventional style automotive air conditioning system that is rated at 5 tons (60K BTUs). It is belt driven off of the engine, with the pulley diameters selected so that the compressor has full output in the engine's normal power range. Now let's say you wanted to wanted to drive this same compressor with an electrical motor. However, you were willing to give up some cooling to use a smaller motor." This was tried on boats to use the engine driven compressor that cools a eutetic plate (brine) for the fridge freezer. The refrigeration is not bothered by the very reduced output as overnight is plenty of time. The problem was the compressor NOISE! ( which is usually covered by a running engine ) was enough to wake most folks . A car compressor will run at 6 to 10HP , size depending , spun by a 3/4 hp AC shore power motor the air would hardly get cool. A DC air cond might work , if you get large batterys. FF |
Nick Badame Refrigeration Co. (Dnick85)
Registered Member Username: Dnick85
Post Number: 286 Registered: 2-2006 Posted From: 70.211.58.172
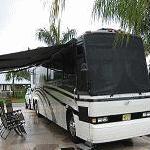
Rating: N/A Votes: 0 (Vote!) | Posted on Monday, April 06, 2009 - 6:56 am: | |
Guy's, I think you would need a clutch on the electric motor just to let the electric motor come up to speed before throwing it at the load of a compressor. Don't forget, your engine has hundreds of hourse power, wheres that tiny electric motor only has it's full HP while up to speed. I don't think the electric motor would have the guts to start an automotive compressor from a dead still. Nick- |
Wec4104 (Wec4104)
Registered Member Username: Wec4104
Post Number: 28 Registered: 7-2008 Posted From: 68.80.242.72
Rating: N/A Votes: 0 (Vote!) | Posted on Monday, April 06, 2009 - 8:29 am: | |
The thought of using two clutches on the set of pulleys was intended so that the two drive mechanisms would not fight each other. When the engine was turning the compressor, the belts would not be turning the electric motor. Certainly wouldn't want the motor to try to crank the diesel. (Message edited by wec4104 on April 06, 2009) |
George M. Todd (George_mc6)
Registered Member Username: George_mc6
Post Number: 774 Registered: 8-2006 Posted From: 64.55.111.6
Rating: N/A Votes: 0 (Vote!) | Posted on Monday, April 06, 2009 - 12:29 pm: | |
Wec, This brought out some interesting comments that I hadn't considered! Tom's idea of letting the electric motor freewheel while the diesel is running would work. I don't see an easy/dependable way to connect the motor to the COMPRESSOR INPUT SHAFT though? The compressor crankshaft would have to be extended several inches, and the back taper for the rear pulley would have to be enlarged so the rear pulley would clear the mount for the front pulley? Then, how do we hold the rear clutch on the shaft, because the bolt in the center is now another 3 inches forward? I suppose the electric could be mounted 180 from the crank to eliminate the concern of a lot of sideways pull on the end of what would now be a long shaft... Then we have Nick's valid concern, which could be solved by starting the motor unloaded, then engaging the clutch I haven't figured out yet. BUT: Proper air conditioning performance is dependent upon sufficient temperature drop (Delta t) across the evaporator coil. Normal stationary equipment drop is 20 degrees, but as the drop decreases, the system will not remove enough humidity, and comfort decreases rapidly. Next problem is that oil circulates with the Freon in all of these systems. The oil is dissolved in the Freon until it goes thru the expansion valve, where it becomes a vapor, along with the Freon. The oil vapor condenses, and is pushed along the bottom of the suction line by the Freon gas flow above it. Now we slow the gas flow down in a large pipe (3 Tons of flow in a 10 Ton pipe,) and the oil will stay in the bottom of the evaporator, instead of being lifted 3 or 4 feet to the compressor inlet, which results in a siezed compressor. That's the reason the driver's air won't work without the coach air on, in most buses. Look closely at Sean's and my posts on 4/3 above! Does that mean that using the driver's air with an automotive size compressor is going to require a smaller condenser, AND A SMALLER SUCTION LINE FROM THE MAIN EVAPORATOR BACK TO THE COMPRESSOR? Yup. I guess you can figure out what Wilbur said? George |
Don Evans (Doninwa)
Registered Member Username: Doninwa
Post Number: 191 Registered: 1-2007 Posted From: 208.81.157.90
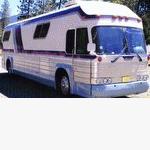
Rating: N/A Votes: 0 (Vote!) | Posted on Monday, April 06, 2009 - 12:55 pm: | |
Just for the sake of discussion, would parallel compressors work? One engine driven, one electric motor driven to simplify the clutches ect. Would let you locate the electric driven in a handier spot than engine compartment. A delay to start the electric motor before the clutch engaged would not be difficult. Would the compressor that is not 'on' leak from high side to low side or want to turn backward? Is there such a thing as an inline check valve or heat pump valve that would solve this? Just curious. Don 4107 (Message edited by doninwa on April 06, 2009) (Message edited by doninwa on April 06, 2009) |
George M. Todd (George_mc6)
Registered Member Username: George_mc6
Post Number: 775 Registered: 8-2006 Posted From: 64.55.111.6
Rating: N/A Votes: 0 (Vote!) | Posted on Monday, April 06, 2009 - 3:37 pm: | |
Don, Valid questions!!! There are indeed refrigerant check valves, and heat pump reversing valves move 4 connections at once. They use a "pilot" principle, and I don't know if one would work in a totally different application than it was designed for. Some scroll compressors did indeed turn backwards immediately after shutoff, until the pressure dropped, and the manufacturers have fixed that now. A reciprocating comp wouldn't have that problem. I would put the electric (and it would be a scroll hermetic,) no way a belt drive, in the compartment with the condenser, to do away with 30 feet of HOT line between the engine comp and the condenser. But we still have the problem of oil return. It just doesn't go where we want it to, it goes according to the laws of physics. We still have a nominal 10 ton evaporator with a header or manifold, whichever, top and BOTTOM, with 3 Tons of Freon gas flow thru it on electic. 1/3 or so of its design flow rate won't lift the oil up to the height of the bus floor, and across to the compressor. I [THINK] the 300+% oversized condenser would work OK, but the expansion valve probably couldn't cope with less than a 3rd of its design flow? Now, flow rate in a chassis engine driven system is all over the place, and is the reason for such a large compressor. This way you still have enough capacity at idle, and the compressor is equipped with unloaders to reduce the load when the evaporator is down to temp. I feel that even if both comps were together in the engine room, teed in right next to each other, (four solenoid valves) that everything would be OK on engine driven. Change over to electric, and the oil will return slower, maybe you lose the electric, change back to engine, and it all comes back in a liquid slug which will destroy the engine compressor. Look above at Sean's post on the system that was in his bus when he bought it: Two engine driven compressors, with two condensers, and FOUR evaporators. (And two siezed compressors) Without seeing the whole setup before the walls were covered, it sounds to me like one evaporator was higher than the other, which would cause more of the oil to lay in the bottom of the low one, while more of the Freon gas went thru the high evap and returned dry instead of oily. Making bus air that works is tough! George |
Don Evans (Doninwa)
Registered Member Username: Doninwa
Post Number: 192 Registered: 1-2007 Posted From: 208.81.157.90
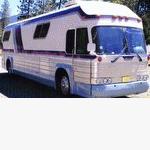
Rating: N/A Votes: 0 (Vote!) | Posted on Monday, April 06, 2009 - 4:51 pm: | |
I don't remember where it was posted but there is a pix of a GM that had two belt driven compressors. My impression was that towards the end of production the factory changed to this system. Teke? May not have been factory, maybe a higher end conversion. Anyway, don't know if they were isolated systems ie front/back or working in parallel. Interesting discussion. Don 4107 |
George M. Todd (George_mc6)
Registered Member Username: George_mc6
Post Number: 777 Registered: 8-2006 Posted From: 64.55.111.6
Rating: N/A Votes: 0 (Vote!) | Posted on Monday, April 06, 2009 - 11:44 pm: | |
Don, It sure is! I remember an ad for a replacement air conditioning system that used two "A-6" compressors, (the GM wobble plate automotive compressor made all during the 60s) instead of the stock comp on many of the GM transits. I don't think it changed the inside portion of the system... George |
Ted Gilbert (Ted01)
Registered Member Username: Ted01
Post Number: 7 Registered: 12-2007 Posted From: 71.60.25.238
Rating: N/A Votes: 0 (Vote!) | Posted on Saturday, April 11, 2009 - 11:03 pm: | |
Boy a lot has happened with the old bus along the way with twists and turns in the last two years or so but we are still heading in a forward direction i think! OK to my point, still haven't done my drivers air.Had time to think about this since my original post in 07, still want to run the compressor off the genny from what i understand a 1hp change out orifice to match, stay with r134, match condensor to that, now if that is right, can i run my original evaporator fans off my invertor so i can still use for defrost? |
George M. Todd (George_mc6)
Registered Member Username: George_mc6
Post Number: 786 Registered: 8-2006 Posted From: 64.55.111.6
Rating: N/A Votes: 0 (Vote!) | Posted on Sunday, April 12, 2009 - 1:37 am: | |
Ted, I'm a little confused. The original evap fans are 24 VDC. I also feel that 1 horsepower won't be enough, when you look at current draw, etc. As posted, a standard automotive compressor will produce considerably more than 1 Ton (12,000 BTU) of cooling capacity. Large roof airs are 13,500 BTU, and if their EER, Energy Efficiency Ratio is 10, they would consume 1,350 Watts. On a hot day, that number will go below 9, and the Wattage will go up. 1 Horsepower requires 746 Watts, so you can see that a 13,500 roof air will consume 2 HP in the real world. Whatever you do, stay with a TXV instead of a fixed orifice. A high and low pressure switch in the circuit is an absolute necessity, in case the condenser fan quits. Finally figured out a cost effective way to properly change over roof airs from inverter to gen, that will be out in a couple of days. Does this help? G |
Ted Gilbert (Ted01)
Registered Member Username: Ted01
Post Number: 8 Registered: 12-2007 Posted From: 71.60.25.238
Rating: N/A Votes: 0 (Vote!) | Posted on Sunday, April 12, 2009 - 9:11 am: | |
Georg Sorry about that. Wan't to run a 110 compressor off the genny direct/or land power, not belt drive.May have gotten off subject a little. Also should have said ,can i run original evaporator fans(or new 110 motors)off my invertor so i can use for heat/defrost? Does this help? Ted |
George M. Todd (George_mc6)
Registered Member Username: George_mc6
Post Number: 787 Registered: 8-2006 Posted From: 64.55.111.6
Rating: N/A Votes: 0 (Vote!) | Posted on Sunday, April 12, 2009 - 11:58 am: | |
Ted, This does make a little more sense, but there is quite a bit to it, especially if you want it to work well! First off, the driver's heat/air/defrost fans are 24 VDC, which is fine with the main engine running. The problem occurs when parked, you need a 24 VDC supply. If you have 24 V house batts, with 24 V charging, and use a converter to power your 12 V house system, you're OK when parked on gen or shore. Otherwise, you will have to provide 24 VDC from 120 VAC to run the evap fans. Or, you can change the evap motor to 120 VAC, and add relays and a 12/24 V inverter to run the evap blowers off the main engine, so you don't have to run the gen in the winter to get defroster. Condenser fan, and compressor power isn't quite so complicated, they can be 120 VAC because they only run in the summer. Personally, I don't feel that a 1 HP hermetic compressor will provide anywhere near enough cooling, the driver's air is a different beast. A roof air has nearly a 2 HP compressor. What are you doing for the rest of your A/C, both OTR and parked? Now you will begin to see why many people use an automotive style belt/engine driven compressor for their driver's air, and generator/shore powered roof/basement airs for the rest. Look closely at Luvrbus's link above... The smaller engine driven compressor will require suction line re-sizing from the main evap back, a smaller condenser and fan, a receiver and accumulator, and a high pressure switch in the clutch cicuit. Good luck, George |
Ted Gilbert (Ted01)
Registered Member Username: Ted01
Post Number: 9 Registered: 12-2007 Posted From: 71.60.25.238
Rating: N/A Votes: 0 (Vote!) | Posted on Sunday, April 12, 2009 - 9:19 pm: | |
george, I have a coleman 2 ton, 2 stage heat pump that I'm going to install in old condenser box, that will be running off the generator or shore. Will have a 24 volt battery bank for house power, with 2 1500 watt pure signwave invertors for house power, along with the generator. So, what you are telling me is that I need at least a 2 horsepower, 110 volt compressor? Have roughly 12 inches in height above the heat pump in the old condensor box. How do i go about sizing condenser for drivers air? |
George M. Todd (George_mc6)
Registered Member Username: George_mc6
Post Number: 790 Registered: 8-2006 Posted From: 64.55.111.6
Rating: N/A Votes: 0 (Vote!) | Posted on Monday, April 13, 2009 - 12:23 am: | |
Ted, In a nutshell, you won't be able to run a compressor the size of a roof air, (13,500 BTU) on a 1500 Watt inverter. THANKS FOR BUYING A SINE WAVE INVERTER, many people don't understand why MSW inverters are cheap! So, if you buy a replacement compressor for a roof air, and all the start components, etc. you will have to run your gen any time you want cooling, or buy a 4000 Watt, 24 V inverter to run the driver's air. Off the top of my pointed head, I would suggest you look at the sizes (and BTU capacities) of the stuff in the Red Dot link I mentioned earlier. Look also at Sean's driver's air setup, because there's an electric that works! Probably a universal replacement condenser for a newer full size pickup will be about right, then you have to get a fan(s) that will move lots of air over it. Please also be aware that an inverter running a 13,500 BTU roof air wil give off about 4700 BTU of heat just by making 120 VAC from 24 VDC. Do you have the Coleman model number handy, and is it an RV type, I hope? I'm still trying to talk you into an engine driven compressor for your drivers air, in case you haven't noticed! Good luck, G |
Ted Gilbert (Ted01)
Registered Member Username: Ted01
Post Number: 10 Registered: 12-2007 Posted From: 71.60.25.238
Rating: N/A Votes: 0 (Vote!) | Posted on Monday, April 13, 2009 - 8:02 pm: | |
George it is basment model,6536B881 Ted |
|