Author |
Message |
Kasse Weikel (More_s_than_as)
Registered Member Username: More_s_than_as
Post Number: 45 Registered: 4-2009 Posted From: 24.205.97.163
Rating: N/A Votes: 0 (Vote!) | Posted on Saturday, June 06, 2009 - 6:37 pm: | |
i currently have my girl up on ramps, i read in the archives that many people do this and you can buy (for bunches of money) pre-fabbed aluminum SERVICE ramps with a pic of the dude under the bus and everything at teh website with NO blocks. so my question is, and im sure other newbs will benefit from this, in your guys' experiences do you find one system is better than the other??? or maybe i should carry around both set ups. i imagine if i wanted to change a tire (which i do have to do) im going to need atlesat one jack i am assuming? right? and since im lazy if any one wouldnt mind repeating info for me...just need one jack i imagine, (i have access to a 12-ton bottle jack) and you just jack it up wherever the suspension meets the axle correct? is that the same for front and back like on a truck (my babies a single axle in the rear)? if i sound like an idiot to you just laugh it off... |
marvin pack (Gomer)
Registered Member Username: Gomer
Post Number: 510 Registered: 3-2007 Posted From: 71.55.197.237
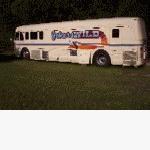
Rating: N/A Votes: 0 (Vote!) | Posted on Saturday, June 06, 2009 - 7:29 pm: | |
KASSE,KASSE,KASSE, NO ONE is and IDIOT on this here BusNut bored. Sometimes we be a actin like one but we not be!!! Now. homemade ramps are probably the best because of the cost. 2x12's are the most common. Now about jacking it up?. A 12 ton low profile bottle jack is just fine. Sometimes the outside dual bites the dust so you can use the ramp to pull the coach on with only the inside wheel on the ramp and you don't have to jack it up at all. Got IT? Always jack on the axle,that way you don't have all the excess of the coach to lift first. Got It? Now if you have to go UNDER the coach,carry some 2x's with you to put under the body so it won't fall and trap you under it. As stated before "When IN DOUBT, BLOCK IT UP" We do not approve on injuries or DEATH'S on this web site.!!! Hope that this helps. Gomer PS ALWAYS BE CAREFUL, THE OLE GAL WEIGHS MORE THAN YOU!!! |
Jim Gibson (River_rat)
Registered Member Username: River_rat
Post Number: 77 Registered: 1-2009 Posted From: 75.95.96.192
Rating: N/A Votes: 0 (Vote!) | Posted on Saturday, June 06, 2009 - 8:44 pm: | |
Kasse, I just jacked mine for the first time - be really carefull! I used a big commercial air-over oil 40 ton, but as soon as I had it up, put 4 5x9 rr ties about 1-2 feet in length under the axel and the body just to be safe. I dont think you have air suspension, do you? If you do, be extra carefull to hold not just the axle but the body so when the bags start to deflate, you still have room. I did this because I was working under there for a week, but even if you are just changing a tire, blocks are a very good idea, especially since a single bottle jack has a lot of pressure on it's small foot, and they can sink into the ground or shift. Obviously, block the tires. Sounds like you're having fun! Jim |
Buswarrior (Buswarrior)
Registered Member Username: Buswarrior
Post Number: 1629 Registered: 12-2000 Posted From: 76.68.122.128
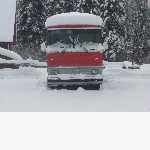
Rating: N/A Votes: 0 (Vote!) | Posted on Saturday, June 06, 2009 - 10:11 pm: | |
Every coach has jacking points. Check the maintenance manual for exactly where those are. Just slinging the bottle jack any old place under there could have it's little top punch through something that was not intended to withstand the jack. Be sure that the jack you carry with you will fit under the jacking points with a flat tire, or you also need a run up block to get it all high enough to lift.... Run up ramps or jacking both have their place, depending on the maintenance job at hand. Having both available at home gives you lots of flexibility. What you choose to take with you on the road depends on a mix of paranoia, experience and how good a Boy Scout you want to be. happy coaching! buswarrior |
R.C.Bishop (Chuckllb)
Registered Member Username: Chuckllb
Post Number: 785 Registered: 7-2006 Posted From: 75.209.213.183
Rating: N/A Votes: 0 (Vote!) | Posted on Saturday, June 06, 2009 - 10:19 pm: | |
Gomer... I AGREE with YOU....mostly, but, in the case of a Crown, Better not block the body...it be Aluminum, 16 gage.....no strength... Crowns have structural members that run from front to rear...but from what I have heard, not many other coaches have that. ERGO... perhaps, block the axles, or other points, as recommended by the mfgr... As you said...always jack on the axle. From my point of view, a proper "ramp"....on the section of the coach where one is "going under" is sufficient, IF there is clearance AFTER the coach "sinks" to it's lowest point, in case of complete "deflation"....and that with careful calculation. ALWAYS BLOCK>>>>is the key! Thanx Gomer for your very careful and thoughtful words of advice! RCB |
Cullen Newsom (Cullennewsom)
Registered Member Username: Cullennewsom
Post Number: 67 Registered: 2-2009 Posted From: 98.201.161.214
Rating: N/A Votes: 0 (Vote!) | Posted on Saturday, June 06, 2009 - 10:25 pm: | |
Never trust a hydraulic jack. |
R.C.Bishop (Chuckllb)
Registered Member Username: Chuckllb
Post Number: 786 Registered: 7-2006 Posted From: 75.209.213.183
Rating: N/A Votes: 0 (Vote!) | Posted on Saturday, June 06, 2009 - 10:27 pm: | |
" blocks are a very good idea,". can't agree there....Mandatory...!!! read the archives about some that did not...post mortem. FWIW RCB |
Kasse Weikel (More_s_than_as)
Registered Member Username: More_s_than_as
Post Number: 47 Registered: 4-2009 Posted From: 24.205.97.163
Rating: N/A Votes: 0 (Vote!) | Posted on Sunday, June 07, 2009 - 1:56 am: | |
ok so then my next question would be, since im sure you guys have already done the research, what did you all find most cost-efficeint for i learned that rounds will split and are no good. jim said he used RR ties. i couldnt even find hard wood blocks and the home depot in carson, i asssume i must go to a lumber mil which is no problem how reliable are tyhese blocks?? use jsut a few or damn near lay a foundation under the bus? im curious to know in order to figure out how many i should get incase i need em roadside. the side of my body appears to be just simple sheet metal skirts that come down, like RC pointed out i think i would be scared to block it on the sheet metal. i got lotsa frame to work with under there though. so once i figure out what kinda wood/blocks to get and roughly how many u guys tend to use for SMALL jobs i can get this tire changed. oh yeah BTW its the fron right tire, thats why i said i assumed a jack would be needed. BW i love your short and sweet answers, they are usually mega helpfull too! i never even thought of special places to put the jack but this makes lotsa sense to me know that u ogt me thinking about it. i once had a POS ford contour that had a jack with a slit in it that slipped on to part of the CHASIS (yers im serious) but it was reinforced around the piece of metal that came down for it. it was a front wheel drive and i never questioned it cause there were blatent instructions and pictures on the side of the jack. im gonna go dig into the manual mac gave me right now! as always thanks for letting me borrow from your experiences and knowledge for i am a lazy one and i know it. |
Mel La Plante (Mel_4104)
Registered Member Username: Mel_4104
Post Number: 119 Registered: 7-2006 Posted From: 99.199.170.124
Rating: N/A Votes: 0 (Vote!) | Posted on Sunday, June 07, 2009 - 10:30 am: | |
one thing that every one should remembeer is to NEVER jack under the axel, always jack at the proper places. the reason for this that the center part of the axel is hollow, it only the part of the spindle that is solid cast. at one time the hollow part was filler with deisel oil so that when a crack developed in the axel you would see were it was leaking out and the wet spot from the deisel oil stays on the axel for a while giving the person that does the look see inspection a chance to see the oil leak and to look for the crack. and yes they do crack and some i have seen have a long one and others just have a star split effect due to someone jacking on the tubing part of the axel, this is caused by the top of the jack post being such a small area it punches a hole or bends tubing which later due to vibtation then become cracks. i have seen a axel that some one had a jack go right into the tube and not a nice thing to get out and no you can not weld a patch on it and then drive with that that way.to those that want to know where the diesel was put into the axel, they took out one of the top bolts holding the steerig unit on the axel out and filled through this threaded hole and then replaced the bolt. |
Buswarrior (Buswarrior)
Registered Member Username: Buswarrior
Post Number: 1632 Registered: 12-2000 Posted From: 76.66.19.245
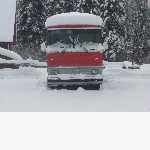
Rating: N/A Votes: 0 (Vote!) | Posted on Sunday, June 07, 2009 - 10:35 am: | |
Under my axle assemblies, on gravel, on each side, I have used a railway tie, to give me a more than ample footprint, with a couple of pieces of 2x8 lumber scraps and pieces of plywood on top to give me the height I wanted. If/when I cut down the railway ties, I think 2 foot long or so would be my aim for a compromise between stable, maintaining some integrity of the wood and easy to handle. 3 or 4 foot and shaped to act as a ramp would be the best of both worlds. As you noted, thought must be given to the manner in which the force/load is applied, (both on top and from underneath) and whether the coach will become a giant wood splitter... layering, using a piece of sacrificial lumber with the grain running in a complimentary direction, between the coach and the rest of your natural wood support would be a good idea. In big transit, for use on a nice flat floor, 1 foot square wooden blocks are fabricated out of 3/4 plywood, glued and bolted through and then painted a bright yellow. In a related manner, a hardwood 4x4 length, cut between 9" to 12", depending on your application, will fit nicely into the axle bump stops to hold up the suspension. Screw in an eye bolt and put a short tether rope on and they are a dream. happy coaching! buswarrior |
George M. Todd (George_mc6)
Registered Member Username: George_mc6
Post Number: 862 Registered: 8-2006 Posted From: 64.55.111.6
Rating: N/A Votes: 0 (Vote!) | Posted on Sunday, June 07, 2009 - 12:04 pm: | |
A little respectful disagreement here. An AXEL is an ice skating maneuver. An AXLE is found under a bus, and other vehicles. What are the spring pads and shackles, etc. in the back bolted to? Couldn't be the axle housing could it? What is the recommended method for towing buses that can't be flatbeded? Lifting it by the axle... Please don't think that I would jack my bus by the axle housing in preference to the bottom shackle plank, that's not what I'm getting at. Now note CAREFULLY BW's comment about "giant wood splitter." Railroad ties are neither hardwood, nor inspected for knots, cracks, etc., and shouldn't be used for life saving support. Close attention should also be paid to his comment on GRAIN. In other words, don't stack a bunch of foot long 2 X 12s all in the same direction, turn every other cut end 90 degrees. Another railroad safety measure, is the requirement for a thin piece of wood between the jack head and the metal underside of the really heavy thing being lifted at its jacking point, which is clearly labeled. This greatly reduces the possibility of the jack slipping out! G |
Bruce Henderson (Oonrahnjay)
Registered Member Username: Oonrahnjay
Post Number: 426 Registered: 8-2004 Posted From: 70.60.107.113

Rating: N/A Votes: 0 (Vote!) | Posted on Sunday, June 07, 2009 - 12:48 pm: | |
Great post, George. Thanks for the clear thoughts. I think of it as two different issues: 1) How do you get the bus up there, and 2) how do you keep it up there safely. 1) If I'm going to look at a slack adjuster, for example, I feel safe putting a "ramp" block (I have a 5 foot railroad tie, cut on the diagonal leaving a 2-foot flat spot) in front of that wheel and driving up on it (but I'm going to rethink that in light of George's comment). THEN, I block using 4X4's in the criss-cross method. And remember, if the ramp breaks or splits or tips over, the amount of force when that bus drops is amazing. Your "blocking" had better be ready to have 10-12-15 or more tons dropped on it and that force is probably going to have a significant sideways component -- in other words, it's gonna want to slide sideways in addition dropping straight down. (I have "steel air" in my suspension's springs so you all do what you have to do about air suspension blocking.) 2) I don't have any problem with jacking a bus (on a suitable frame point, of course) into the air. My bus has solid beam axles but (in line with Mel's thinking) I don't see any benefit to putting a bend or dent in them anywhere. There are flat suspension bosses on my front axles (the rear one is really weird - gonna have to go have a good look at that one). But, in my mind, jacks are *way* more likely to cause trouble than a roll-up ramp. Lift it, but immediately -- before you do anything else, block under the frame (and in your suspension, if necessary). My own preference is to jack, block and then release the jack so that the weight of the bus is fully on your blocks. If the jack slips and your bus is half an inch above the blocks, the bus frame will hit those blocks onehelluva jolt and that's a jolt that I'd prefer to avoid. I'd appreciate anyone's thoughts on this. I've been lucky enough to have a concrete pad to work on so far. But remember, a jack or runup ramp or blocks aren't any better than the surface that they're sitting on. Even with cars, it's often hard to get a big-enough, solid-enough board on the ground and still have room between that and the jacking point, especially if you have a flat. If you're not a totally reliable surface, you MUST take that into account and prepare a solid, reliable surface for your ramp, jack, or blocks to sit on. Sorry, I've babbled on here but I meant for my point to be that you have to be safe -- getting it into the air AND holding it up there, and sometimes these are two different situations. |
marvin pack (Gomer)
Registered Member Username: Gomer
Post Number: 514 Registered: 3-2007 Posted From: 71.55.197.237
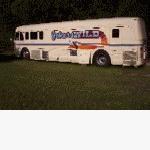
Rating: N/A Votes: 0 (Vote!) | Posted on Sunday, June 07, 2009 - 2:21 pm: | |
I forgot to mention something!![ senior moment]. I carry a piece of flat steel somewhere about 2x2 just for jacking on dirt. It is a little thicker than 1/4 inch and worked perfect every time. If space is a problem in carring a lot of wood try a steel plate. I also have some 3/4 oak strips that I use for putting on TOP of the jack. I be a trying to thunk up all this hear stuff at one time and I can't do it.LOL. I be a trying tho!! gomer |
George M. Todd (George_mc6)
Registered Member Username: George_mc6
Post Number: 864 Registered: 8-2006 Posted From: 64.55.111.6
Rating: N/A Votes: 0 (Vote!) | Posted on Sunday, June 07, 2009 - 2:54 pm: | |
Bruce, There's no "babbling" here, its all well thought out, and makes sense! I like your comment on "steel air," yours won't settle on you/squish you slowly, like most of our murrikins. Your axles will rise much sooner when you raise the body, than those of an air ride bus, and you don't have to worry about the weight of the wheels and axles hanging on old air bags! "Suitable frame point?" Exactly! This is no joke, a guy I worked with in the late 60s, worked the day shift, and came out at 4pm to find a flat rear tire. About 445, he came in mad and yelling to us on the swing shift about the @#$%&* jack being in the way of the tire. Five of us couldn't figure out what Doug was talking about, and went out to look. Sure enough, he had put the bumper jack in the middle of the wheel well, and jacked the car up. The car had good fenders, the only thing crumpled was his ego, when we all explained it was a "bumper jack!" Now I'm babbling, Regards, George |
Bruce Henderson (Oonrahnjay)
Registered Member Username: Oonrahnjay
Post Number: 428 Registered: 8-2004 Posted From: 70.60.107.113

Rating: N/A Votes: 0 (Vote!) | Posted on Sunday, June 07, 2009 - 7:07 pm: | |
Good idea on the steel plate, Gomer. Sounds like a good solid base without getting into your "ground clearance" too much. I wonder if it's worth welding little cleats the size of your jack's base on it (i.e. weld a "box" of like strip steel or rebar that the jack fits into); another slip prevention idea. |
Mel La Plante (Mel_4104)
Registered Member Username: Mel_4104
Post Number: 120 Registered: 7-2006 Posted From: 99.199.170.124
Rating: N/A Votes: 0 (Vote!) | Posted on Sunday, June 07, 2009 - 7:41 pm: | |
heck i do not mind the dis agreement at all, as stated there are all those things bolted to the axel with a great surface area where contacted to the axel. if you want to use the under side of them it works fine. i use a large piece of channel that is 3/4 in. thick and 12 in. long .in the center of the channel on the flat side i welded a piece of pipe about 1 in. long that is just bigger than the top of the jack post so the jack will not slip off when jacking. i would not use a piece of wood regardless if it is hardwood or not betwen the jack mast and the axel as the wood will compress and bend or split. but as FF will say do it your way. |
FAST FRED (Fast_fred)
Registered Member Username: Fast_fred
Post Number: 820 Registered: 10-2006 Posted From: 76.195.79.226
Rating: N/A Votes: 0 (Vote!) | Posted on Monday, June 08, 2009 - 6:34 am: | |
Most common woods will take about 4000 psi per sq inch before crushing , so placing the coach on at least 1 sq ft of lumber has a good safety margin. Ramps should be the thickness that will slide under the bus , when aired down. A coach with rubber or steel springs can use thicker lumber for the ramp. FF |
marvin pack (Gomer)
Registered Member Username: Gomer
Post Number: 517 Registered: 3-2007 Posted From: 71.55.197.237
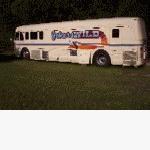
Rating: N/A Votes: 0 (Vote!) | Posted on Monday, June 08, 2009 - 8:15 am: | |
Bruce that wouldn't bother a thing to weld a cleat on the plate and I never done this but weld up a piece that will fit on top of the jack to fit the axle and that way it wouldn't slip. I would put a piece or rubber on it also. I jacked the MCI up and pulled the wheel on one side with the set-up and left it for at least a week while working on it along with blocking the body too and it all stayed in place and was SAFE!!! Gomer |
Bruce Henderson (Oonrahnjay)
Registered Member Username: Oonrahnjay
Post Number: 429 Registered: 8-2004 Posted From: 70.60.107.113

Rating: N/A Votes: 0 (Vote!) | Posted on Monday, June 08, 2009 - 9:20 am: | |
Sounds good, Gomer. I like your idea of the notch in the jack to grip the axle, and the piece of rubber. Metal to metal is incredibly slippery, hence the note about about a piece of wood between the railroad jack and thing being lifted. And of course, on the road, Murphy's Law says that you'll be in the worst place with the softest surface in the baddest light when you need to jack up your bus. |
Jim Gibson (River_rat)
Registered Member Username: River_rat
Post Number: 82 Registered: 1-2009 Posted From: 75.95.96.192
Rating: N/A Votes: 0 (Vote!) | Posted on Monday, June 08, 2009 - 10:44 am: | |
Kasse, If you are in Carson area, drive a bid furthur south from Home Depot on 395, and just after Airport Road is Genoa tree farm. The ties I bought there are really clean and never used - I think they were left over from a narrow guage RR. They are 6' X 5 1/2 X 8" or so and are beautifull clear-heart redwood. In cutting them, I never saw a knott and with the bus on them, they never exhibited any signs of splitting or "unhappiness" - really good wood, and even though redwood is soft, being clear heart, it is fantastic. Also, they are only $10 each! If you do get over there, I'm just 20 min furthur south in Gardnerville - stop by and I'll show you my project. Jim |
R.C.Bishop (Chuckllb)
Registered Member Username: Chuckllb
Post Number: 791 Registered: 7-2006 Posted From: 75.208.77.217
Rating: N/A Votes: 0 (Vote!) | Posted on Monday, June 08, 2009 - 11:12 am: | |
I thought I had posted this yesterday, but can't find it...if this is a repeat, please forgive.. (maturity setting in..again!) When I took delivery of our coach along with it were about a dozen 14 inch square x 1 1/2 inch thick Marine plywood well used, oil soaked, heavy blocks. Not a sign of distress, cupping or deterioration...just filthy so I put them to the fire. Clearly had been much used over the years( 1964). University of Northern AZ did a most of their own maintenance work and records show tire changes, etc "in the field". My guess is that the blocks were "key" to that purpose. They were easy to store, didn't take up a lot of room in the bay, and stacking made hauling them around no problem. FWIW RCB |
PA Doug (Padoug)
Registered Member Username: Padoug
Post Number: 7 Registered: 1-2009 Posted From: 76.120.147.169
Rating: N/A Votes: 0 (Vote!) | Posted on Monday, June 08, 2009 - 11:42 am: | |
This is what I will be looking into getting. I may have found a bus, but first I need to see if there are manuals for it. Second thing is a good set of ramps so I can learn all I can about whatever we do end up buying. I want something commercial grade that is easy to store and designed for my use. The company is in the Pittsburgh area. https://www.dambachramps.com/scripts/prodview.asp?idproduct=2472&idCategory=70 |
Peter E (Sdibaja)
Registered Member Username: Sdibaja
Post Number: 298 Registered: 5-2002 Posted From: 201.171.230.132
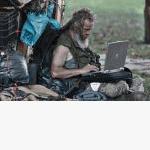
Rating: N/A Votes: 0 (Vote!) | Posted on Monday, June 08, 2009 - 1:09 pm: | |
I think those one piece metal ramps would be a real PITA and a waste of resources. I carry a bunch of various sized cutoffs: 2x4, 2x6, 4x4, 6x6, 4x12, plywood scraps, etc. Stack to suit the occasion (cross slope, etc) and make a ramp of them if wanted, drive a foot or two, re-stack, etc. NEVER use a wood block on end, it will split. NEVER use concrete blocks, no strength and they fail all at once. An assortment of wood blocks can be stacked and nested around your other gear in the bed/bay/trunk. and will be handy for leveling the rig too. Hardwood/Softwood... no preference. I prefer the Doug Fir that is a common building material out here in the West, but there is very little practical difference. Watch the crush as the weight goes on, take your time, have plenty of extra blocks at hand at all times. |
R.C.Bishop (Chuckllb)
Registered Member Username: Chuckllb
Post Number: 792 Registered: 7-2006 Posted From: 75.208.77.217
Rating: N/A Votes: 0 (Vote!) | Posted on Monday, June 08, 2009 - 2:39 pm: | |
PADoug,,,my point of view is that these shown are overkill for a hobbyist.,,,ever consider the weight of those? Mine are 10 inches wide x 8 inches high by about 4 feet in length...all I want to move around, and then some. DIYW FWIW RCB |
RJ Long (Rjlong)
Registered Member Username: Rjlong
Post Number: 1571 Registered: 12-2000 Posted From: 98.192.173.82
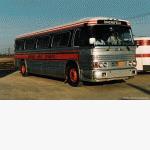
Rating: N/A Votes: 0 (Vote!) | Posted on Monday, June 08, 2009 - 3:37 pm: | |
Kasse - Everybody's missed the fact that you've got a Gillig Phantom Transit bus. As you've seen by looking underneath, the Phantom's got two massive frame rails that run the entire length of the coach, and everything's hung off those rails. There are no jacking points on the body of the coach itself, as it's just a box huck-bolted to the frame. If you don't have access to a hoist (few of us do), you can use an air over hydraulic jack to lift the coach using the frame rails front or rear. If you wanted the chassis such that the front & rear suspension hangs free, you'll have to crib up blocks high enough to support the vehicle on the frame rails. At the back axle, if you've got the suspension type that has a single air bellows located behind the duals, IIRC you can jack the coach up using the trailing arm. Since the Phantom is still in production, you could call Gillig's service dept to confirm the proper way to jack up the coach: 1-800-630-4070 or 1-510-785-1500. And, just in case you need some, their parts department is 1-510-264-5160. FWIW & HTH. . .
 |
Kasse Weikel (More_s_than_as)
Registered Member Username: More_s_than_as
Post Number: 54 Registered: 4-2009 Posted From: 24.205.97.163
Rating: N/A Votes: 0 (Vote!) | Posted on Monday, June 08, 2009 - 3:46 pm: | |
hey doug - i must sorrowly agree that those ramps mahy not be the way to go. although those one are MUCH cheaper than the ones i was finding online, i made my ramps out of 10x2 (the tire seems to be just less then 10 inches wide) and it only costed me 50$ for each SET (yeah i built 2 sets for the back cause i gotta crawl under there and im paranoid). although my ramps for the outer wheels which has a bottom board 8 feet long are kinda heavy...i jhust grab the light end and drag the heavy end around. im thinknig of maybe installing wheels on them to when i tilt em pass maybe 30 degrees the wheels touch down and i can move em like that. its super easy to build your own and i asked "pros" at 2 different lumber yards about my double set design and they both said "30,ooo pounds? thats it?!?" (yeah i just rounded up from 26,000 to make sure). and yes they BOTH suggested doug fir as well for weight/strength reasons. |
Dave (Virtual)
Registered Member Username: Virtual
Post Number: 34 Registered: 5-2009 Posted From: 67.186.253.131
Rating: N/A Votes: 0 (Vote!) | Posted on Monday, June 08, 2009 - 11:25 pm: | |
If your phantom is like mine, there is a huge space between the frame rails in front of the rear axle. Additional huge spaces outside the frame on each side. I believe the lower panels are partly for looks and partly to keep cars from going under. If you take off one of the lower panels and put a rack, you could put your ramps there and then you could fit your water tanks under the bed or wherever it was you promised to the ramps. For my use, I can't see any other configuration than a twin bed down each side with a water tank underneath. You'll need that floor access plate open for your daily brake checks. Right RJ? And of course, every one of those signs that says "check brakes," means you are supposed to crawl back there and verify the adjustment. You'll be more likely to do it if you can lay on the floor than if you have to crawl under. Just a thought. You could also build a huge basement (relatively speaking) behind those lower panels. The space is about 16" or 18" high by about 31" deep IIRC. Picture about 15' of "toolboxes" hanging under each side. I think you could figure out something below the floor and between the frame rails but I haven't looked into it. I'm picturing a trap door in the floor as I'm surely not going to be crawling around underneath. Finally, for your "road ramps" I'd consider something where all the boards aren't permanently fastened together. Someone suggested vertical holes for inserting a bolt or reinforcing rod. |
joe padberg (Joemc7ab)
Registered Member Username: Joemc7ab
Post Number: 351 Registered: 6-2004 Posted From: 66.38.159.33
Rating: N/A Votes: 0 (Vote!) | Posted on Thursday, June 11, 2009 - 2:34 pm: | |
Padoug I Would not look seriously at the ramps in your post. In the upper right hand corner shows the underside of those ramps and they are hollow. So unless they are used on a heavy concrete floor they are allmost useless. On asphalt they will sink like a knife in warm butter, never mind what they would do on gravel or dirt. Steel ramps on concrete also have a tendency to slide when try to drive onto them. Use the suggestions of the other posters in this thread and you will be better of (safer) and save a bunch of cash as well. Joe. |
Kasse Weikel (More_s_than_as)
Registered Member Username: More_s_than_as
Post Number: 57 Registered: 4-2009 Posted From: 24.205.97.163
Rating: N/A Votes: 0 (Vote!) | Posted on Saturday, June 20, 2009 - 6:23 pm: | |
RJ - good call on calling the gillig people thanks for the hot tip! i saw online as well that they are still making busses but the new ones are a lot different looking |
|