Author |
Message |
bill keel (Crptklnr) (198.81.20.187)
Rating:  Votes: 1 (Vote!) | Posted on Sunday, February 09, 2003 - 7:00 pm: | |
Hi, A few thoughts on RTS modifications. Could a steer axle module be "spliced" between the drive axle and engine modules to create a 45' 3 axle RTS? Also, some input on raising the roof by spliting the body below the windshields, clam-shell style? thanks, bill. |
Mike Stabler (Docdezl) (64.255.109.207)
Rating: N/A Votes: 0 (Vote!) | Posted on Sunday, February 09, 2003 - 8:21 pm: | |
OK so I was lookin at an RTS camped across from us and after one (3) martinis seated in a lawn chair. Holding my arm out with my thumb up pointed toward the RTS "coach" sighting with my laser eye. I burnt a line .006" below the floor the length of the "coach" and lifted and held. From the "envy" section of my memory I pulled the bays of an H3-40 complete with 24" alcoa's and cut and paste under RTS upper section. Didn't loose a single olive? Smoke,rattle&,stink.....docdezl |
Dwight (67.213.8.1)
Rating: N/A Votes: 0 (Vote!) | Posted on Monday, February 10, 2003 - 1:16 am: | |
Hi Bill Would it not be easyer to put a drive axle module in front of the current drive axle, install a U-shaped steer axle where the current drive axle is and add what ever you wish to raise it, between the rear and front frame and structure ??? then you would just have to add that amount to the lower outside of the bus (less outside work) .... that would give you, what ever you added between the structure and frame, to the bays in added height ... then you would just drop in you favorite "T" Drive drive train !!! |
Skorpio (Skorpio) (24.92.193.195)
Rating: N/A Votes: 0 (Vote!) | Posted on Monday, February 10, 2003 - 3:02 am: | |
There is a really good group for RTS issues at http://autos.groups.yahoo.com/group/RTS-bus-nuts/ they are very knowledgeable about the RTSII. Although there is a large number of the members that have been there done that, most of the advice will amount to how to assimilate your shell into the flock, which is probably good advice for 99.9% of the cases. I too am very curious about the RTS and its modular construction and what can be done with it. Asked in a manner that did not make my intentions too obvious I've been able to find out the following info that you may find helpful. 1) The RTS is constructed out of 5 foot long unitized body sections or modules, with essentially a nose cap and a powerpack tail cap on the ends. 2) The modules are welded together with a substantial number of welds. 3) There are unique bulkheads from the bottom of the bus to the floor level between modules, these bulkheads are available as service parts and are designed to be replaceable, they are not just bolt ins however. 4) There seems to be 2 sub frame assemblies, one that is contained within the steer axle module and one that extends from the rear bulkhead of the rear axle module through the front bulkhead of that module and continues to the next forward bulkhead under the module that normally contains the rear door and wheelchair lift. 5) Depending on the year, some RTSs have a double A arm independent front suspension and others have a solid drop axle. 6) The welding faces of all the mid modules are the same front and rear. So the jig that originally put these buses together makes essentially the same welds in the same places between all modules. The 5 foot axle modules (subframing and bulk heads aside) are obviously unique but from an assembly stand point are designed to be "stacked" into the structure like any other mid module. 7) The RTS uses a transverse mounted engine connected to a Allison V-730 or V-731 3 speed automatic transmission which puts the output shaft at about 60 degrees off parallel to the engine and feeds into a Rockwell axle with a matching pinion angle. From an engineering stand point, you could add a front axle module between the powerpack/tailcap and the rear axle module. The original driveline could not be used, the transmission output angle and pinion angle would not even be close after you add 5 feet in between them. However you would gain enough space to put just about any engine and trans combination you wanted connected to a 90 degree pinion. The Rockwell axle may be able to have the differential carrier swapped out to archive this (I haven't been able to get this info yet) and if it can, there is a high likelihood that if it is possible it is also available as a 2 speed carrier as the axle model that seems to be in the same series has that option. So there seems to be the possibility of using a 4 speed Allison with a 2 speed axle giving you 8 forward gears. The engine compartment, if isolated to the tail cap would be large enough to fit an 8V-92 or maybe even a 12V-71. There would be ample space for a transmission between the tag. You would have 4 feet or so from the back of the engine to the point that the output shaft would need to be to still have enough room for a drive shaft if the engine ended at the last bulkhead. The trans would need to sit inside of a structural frame of some sort to provide the lateral strength needed for the tag. The IFS front module seems like it would be the one to use since the options for structure seem more open. The possibility exists for making that a passive castering (steerable) tag, ot just locking it into place. Making it liftable seems unlikely. As far as a roof raise, the construction and shape of the RTS makes that a major undertaking, this coming from someone that thinks the re-powered stretch is doable. The RTS is too rounded to easily raise (an intercity is vertical on the sides you just cut, raise and fill the gap. An RTS would require a lot of re-engineering of the fundamental structure to do a roof and/or floor raise on. The basic structure of the RTS is like a unitized automotive body on a grand scale and modularized into standardized mass producible pieces, only a big 3 auto manufacturer could come up with a design like this. Who else could reduce a 10x8.5x5 foot section of "bus tubing" to a basic part. The sub-framing sections are somewhat more traditional (sort of) so I think the stretch re-power thing could be done by someone with a good engineering mind so as not to exceed the structural limits of the basic chassis. A roof raise would have to consider 25 feet of torsional body twist on resulting modified structural "tube" that the RTS is. The only place that you could probably get away with cutting the RTS and raising it would be at floor level and inserting an "H" shaped structure that would allow you to stack another row of bays on top of the existing ones and raise the roof by adding wall height at the bottom. You could then cross brace under the floor at the module boundaries to gain back the reduced structural rigidity. What all this does to the look of the RTS is another thing. You would either end up with an RTS styled scenic cruiser kinda bus by raising all but the nose, or a big slab front that makes it look like an intercity anyway so why bother. By the time you got done it would not be cheaper than converting an intercity, so you are doing this because you like the RTS look. It would take a lot of engineering and a lot of design talent to raise an RTS and not compromise the look. I can't see doing this if the look isn't paramount to your objective. I personally have loved the look of the RTS since I first saw one 20+ years ago, and have had thought it would make a great RV from the beginning. I've only recently be enlightened to the fact that it is indeed a popular platform for this. Regardless of the costs involved the RTS is what I would choose for the base of my project. I can live with the limits of its volume in order to get the look. |
RJ Long (Rjlong) (24.127.74.29)
Rating: N/A Votes: 0 (Vote!) | Posted on Monday, February 10, 2003 - 4:37 am: | |
This is an interesting thread! Awhile back on one of the bus BBS's there were comments quoted from a GM/TMC/NovaBus engineer regarding the installation of a 4-cycle T-drive powertrain in the RTS shell. There were two findings that surpised the engineering staff: ~ The amount of vibration found thru-out the vehicle with the 4-cycle motor. (A Cummins, IIRC. Or maybe it was an S-50 DDA. . .) ~ Chassis stress fractures. I don't remember if it was concluded that these fractures came from the 4-cycle motor, or from the weight of the powertrain being supported differently from the original V-drive. Wish I could recall where I read this. . . maybe someone archived it?? If so, might be worth re-posting under this thread, simply for additional input into the ideas being presented. RJ PD4106-2784 Fresno CA |
Geoff (Geoff) (66.238.120.121)
Rating: N/A Votes: 0 (Vote!) | Posted on Monday, February 10, 2003 - 6:58 am: | |
Hi, RJ-- there is a letter in the files sections of the RTS Yahoo group that may be the one you are refering to. Also, a few years ago we had one guy who raised the roof and the floor on an RTS and tried to make a commercial enterprise out of the process. The business fell apart and someone ended up with an unfinished and unique RTS. You can get an idea of what he did by reading the old archives in Randy's Go-Wheels site: http://www.gowheels.com/rts/ The problem with raising the roof and floor was by the time he was done it no longer looked like an RTS. The way the bus is designed at it's 10 foot height it has a wonderful center of gravity that is lost if you raise anything. To me just doing a conversion is enough work without doing major structural changes.... --Geoff '82 RTS CA |
bill keel (Crptklnr) (198.81.20.38)
Rating: N/A Votes: 0 (Vote!) | Posted on Monday, February 10, 2003 - 7:16 am: | |
Hi, My primary thought was to gain interior floor space and convert to a T-drive. the roof raise was an after-thought. The idea of an RTS-based "sports car" conversion really jazzes me! Only a few years to retirement, so better do more homework! Thanks for your input, all. Bill |
Skorpio (Skorpio) (24.92.193.195)
Rating: N/A Votes: 0 (Vote!) | Posted on Monday, February 10, 2003 - 7:53 am: | |
Yes, this discussion is posted on the RTS yahoo group and often quoted. But bear in mind that an in-service transit will see more abuse in a month than most of the buses here will ever see. The engine that was tested was almost certainly the S-50 which from what I understand makes a paint shaker seem smooth (low idle and only 2 firings per crank rotation and lots of reciprocal weight). I can only assume that a T-drive would shift the weight center of the power pack way aft of the axle. Am I right in assuming that T-drive is a nomenclature for longitudinally mounted engine or traditional engine-transmission-drive shaft-pinion arrangement? On the other hand that same discussion with the GM/TMC/NovaBus engineer eluded to the fact that cutting up the bus into modules and re-welding it was a routine operation at the factory and seem to hint that some of the transit companies did it as well. A 2 stroke re-power with a tag axle should be able to be constructed to actually reduce the stress on the chassis over the factory power pack, since it would move the weight center much closer to the center of a weight bearing axle (tag axle was not part of the service duty re-power equation) and removal of the half ton air conditioner above the power pack and the wheel chair lift would further reduce the stress on the chassis. Converters have a lot of luxuries that were not available to the factory re-power programs. |
CoryDaneRTSIIIL (4.17.253.69)
Rating: N/A Votes: 0 (Vote!) | Posted on Monday, February 10, 2003 - 7:06 pm: | |
I would only comment on the moving of modules in the RTSII. OK, lets talk welds, as you RTS owners know, GM does not beleive in spot welds, especially in the framework. They are long deep welds that go from below the floor up the wall across the ceiling down the other wall and below the floor again which form that tough unibody (sort of)construction. IMAGINE trying to separate the weld, of stainless steel, without destroying the structural integrity..... The bus that was raised was raised floor and all, adding frame work and storage under the floor. His cuts were across the structural member, like you would cut a board, not longitudally along the length of the structural members. Another thought to be considered is what changes to metal strength will occur after you cut off all that weld and try to weld again in a new position. GM used robots that were timed for precise heat and cooling times on new metal stock, so to not modify the tensile strength of the structural metal. Obviously, we have no knowledge of what it would entail for us to do the exact same thing even if we were using new metal, but in this case it would be MODIFIED metal. I think if you would go ahead in the direction of cutting up the bus and adding sections, you should not be talking to us, you need a structural engineer and a metalurgist to know how to do it safely, if it can be done without destroying the structural integrity of the metal you are cutting up to separate sections. I'm not saying don't do it, I'm saying make sure it can be done. just my thought - cd |
Skorpio (Skorpio) (24.92.193.195)
Rating: N/A Votes: 0 (Vote!) | Posted on Tuesday, February 11, 2003 - 12:46 am: | |
See this is my point, when someone suggests cutting a section out of an RTS to do a re-power or lengthen it, or change the transmission or anything of that sort you get told how difficult it is, yet the topic of cutting out a section to make a 102" wide 35 footer is greeted as "shouldn't be that difficult to do". This doesn't make any sense. From what I've been able to collect on the subject, the RTS is made out of the Stainless alloy it is because the heating/cooling stress is not that critical. The RTS is made of 409 stainless which has pretty neutral heat properties as far as stainless goes, has very good weldablity characteristics, no nickel content, this particular stainless steel alloy was developed to be easily cut, heat formed and welded and was originally developed for automotive exhaust systems. It is particularly resistant to tensile variations caused by heating and cooling. Robotic welding particularly in the early days of the RTS was not the strong suit of the American automotive manufacturing industry, this is why the Japanese auto makers gained so much ground during this time (late seventies early eighties). American automotive robotic welding technology was notoriously bad and inferior in almost every way to the laid off UAW welders they replaced. I am well aware of the "Big Bertha" rig that the RTSs where assembled on but we are talking about a device that was christened in the mid seventies when IBM mainframes had 512K of spinning core memory running on a flywheel generated clock. High tech precision this ain't. Robotic welders of that time period were lucky to plot their programmed course without screwing something up. I can just about guarantee that robotic welding was used on the RTS not because anyone at GM thought it was superior but more likely because at a 20 year production yield of around 20,000 buses it was cheaper than paying loaded salaries to a journeyman UAW crew for a low production vehicle. Way too much idle time on the line to pay veteran union workers. The fact that GM used a plotted course robotic welder to join the sections of the RTS during that time period is amazing, and only attests to the forgivability this alloy has. I am an engineer by trade and have a very good understanding of structural, mechanical and electrical engineering as well as metallurgy. |
Wulf P. Ward (63.155.8.128)
Rating: N/A Votes: 0 (Vote!) | Posted on Tuesday, February 11, 2003 - 9:01 pm: | |
All this talk about t-dives got me going. About 4 years ago I did buy the last of the Flxible buses. One was a demo-bus and 2 were just off the line and one was not all together. The last 3 did not have VIN #'s yet. This were brand new buses. Two had 8.3 Cummins with Voight t-drives and two had 8.3 Cummins with Voight angle (v-drives)drives. All of them got by on 2 axles. The t-dive models had a larger rear overhang. I think anything can be done and I was thinking in the same direction for a while. I was going to raise the bus 10" and cutting it right under the windows (that's the only straight part of the bus). The front will be a little of a problem, but it would have to be cut just under the windshield whipers at the point were the front-end sticks out the most. For the back I was thinking about not raising it, but just framing up to the last section and bringing the rear cab up and adding the 10" to the cab. Why 10", because that is the driver petestal hight, so the drivers area could stay were it is. Also 10" would only add 1 step, at the upper landing, going to the back of the bus. Also the door could stay the same, with just a filler over the door. Some converters like to go 14" to come over the fender wells, but I think it will be to much. Somebody converted an RTS into a furnature display van and raised it 36" to 13.6' It still looks like an RTS with a cone shaped roof. Also somebody welded 2 RTS buses on top of each other, with loft type bed rooms for his the kids. It looks a little crazy, but it still does look like an RTS. To make that RTS look go away, one would have to make some big changes, like covering the front, but why?? Around here kids make low-riders out of Jeep Wranglers and go-carts out of Hondas, so I am used to crazy stuff. Geoff said it right, why add more work to a big enough job allready. |
Perry W Munger IV (64.81.112.30)
Rating: N/A Votes: 0 (Vote!) | Posted on Thursday, February 13, 2003 - 12:08 am: | |
This double RTS is intriguing. I've heard mention of it. Does anyone know where I can get info on this monster? How badly does it hobble the bus in the handling department? |
Pete RTS/Daytona (68.128.144.243)
Rating: N/A Votes: 0 (Vote!) | Posted on Thursday, February 13, 2003 - 8:34 am: | |
Hmm - let me see if I can post a picture from the Yahoo-RTS-bus-nuts photo pages
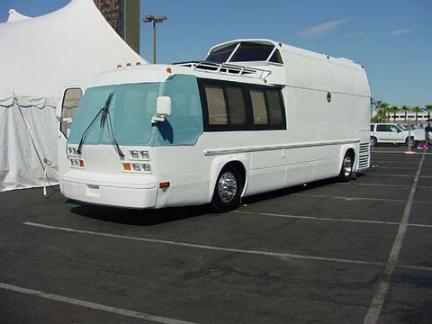 |
Buswarrior (Buswarrior) (64.229.213.34)
Rating: N/A Votes: 0 (Vote!) | Posted on Thursday, February 13, 2003 - 5:00 pm: | |
RJ, I remember the vibration post too. I was somewhat involved, since we've got some RTSII DDEC S50, VR-731R drive trains and some D90 Flyers with Cummins L10 V-730 set-ups here at the local big transit company. The direction of that thread was to line up the donor transit for that modern drive train swap. I seem to remember that FastFred brought in the Nova engineer details that the switch to 4 stroke from 2 stroke in the RTS caused all sorts of unexpected vibration related structural problems throughout the coach. Maybe last fall? happy coaching! buswarrior |
Marc Bourget (209.142.38.81)
Rating: N/A Votes: 0 (Vote!) | Posted on Sunday, February 16, 2003 - 7:47 pm: | |
Pete Plaskove was the builder who raised the suspension and floor. I saw it at Pete's house before he sold it to Marv Gunnafson (Tustin, California) who now has the chassis and is putting it back together. Pete pretty much stripped the hardware out of it so a lot of fundamentals had to be replaced. About the S-50 installation in the RTS, the reason (probably true!) the chassis cracked is that the vibration on the 4 cyl engine is so severe, due to an approx 11 litre engine, 4 power pulses instead of 6, and the inherent vibration characteristics of a 4 cyl. engine. This type of swap needs much softer engine mounts. The MCI S-50 installation allows total travel right to left at the top of the engine of about 4" according to my sources. The RTS chassis would have to be reinforced in addition. There is room for a 12V71 in a T-drive configuration. The original RTS design study received a contribution from the military for a 4WD-AWS Troup Transport version using that engine. The prototype worked well but couldn't pass the sideslope test. Onward and Upward (The original...) "Marc" Bourget |
Dwight (67.213.8.131)
Rating: N/A Votes: 0 (Vote!) | Posted on Saturday, February 22, 2003 - 9:31 am: | |
HI Marc Are you saying a 12v71 T drive in a RTS ??? |
|