Author |
Message |
Matthew J Rutkowski (Matt_rutkowski)
Registered Member Username: Matt_rutkowski
Post Number: 5 Registered: 1-2010 Posted From: 71.207.42.146
Rating: N/A Votes: 0 (Vote!) | Posted on Thursday, April 15, 2010 - 10:25 pm: | |
I picked the 6 up tonight at the diesel shop after an inframe overhaul. She ran perfectly the 60 miles to my home however just as I left I noticed the 24 Volt meter was only reading 23 to 24 and prior to the overhaul it was putting out 28V. What do you guys think might be the problem? I am guessing a ground somewhere?? |
David Guglielmetti (Daveg)
Registered Member Username: Daveg
Post Number: 161 Registered: 2-2009 Posted From: 71.139.247.230
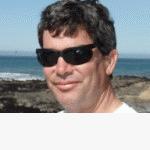
Rating: N/A Votes: 0 (Vote!) | Posted on Thursday, April 15, 2010 - 11:08 pm: | |
Certainly would be worth checking (visually) the wiring around the alternator...maybe at the starter too. If you find anything out of place, keep looking...maybe something else was overlooked also. Time to get your battery charger out! |
Gary Pasternak (Cessna5354)
Registered Member Username: Cessna5354
Post Number: 81 Registered: 2-2007 Posted From: 71.254.59.159
Rating: N/A Votes: 0 (Vote!) | Posted on Friday, April 16, 2010 - 5:21 am: | |
Could possibly be the batteries are down if in the shop with small loads over a period of time. I have 2 8D's and they charge, but slowly, I would check the voltage of the alternator(generator) at fast idle to verify the panel meter. Get the batt's charged & drive it again. Good Luck |
John MC9 (John_mc9)
Registered Member Username: John_mc9
Post Number: 1120 Registered: 7-2006 Posted From: 74.162.65.206
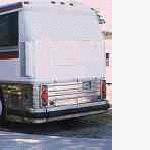
Rating: N/A Votes: 0 (Vote!) | Posted on Friday, April 16, 2010 - 9:16 am: | |
According to der bookle, the batteries should be charged at a rate that produces the least amount of water loss (boil-out). On my 9, that was around 24vdc; at 27+ volts, the batteries would have to have water added after each trip or extended run-time. If you had the diesel shop do an in-frame overhaul, did they also reset the regulator to the proper setting for you? You didn't say the batteries were dying, you said you just thought the charge rate was too low....... Maybe it's now set at what it should have been... |
Sean Welsh (Sean)
Registered Member Username: Sean
Post Number: 1074 Registered: 1-2003 Posted From: 70.134.90.221
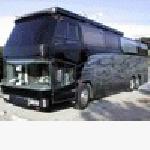
Rating: N/A Votes: 0 (Vote!) | Posted on Friday, April 16, 2010 - 12:00 pm: | |
I don't know what "bookle" you are looking in, but batteries will not charge at 24 volts. A resting battery voltage reading of 24 would mean the batteries had only 25% of their charge (fully charged batteries, by contrast, would read 25.4 volts), and if your charger is only putting out 24 volts at its maximum setting, then 25% charged is as far as the batteries will ever get. In practice, it will be less than that because of the way batteries charge. "24 volt" battery chargers need to be set to a minimum of 26 volts to fully charge in any amount of time, and the standard setting for 24 volt alternator regulators is 28.0-28.6 volts. If you are concerned about excessive water loss, then set your regulator to the lower end of that scale, around 28.0. But understand that all flooded batteries lose water; if it's not losing water, it is not charging properly. Expect to add water to flooded batteries at least weekly in daily use. To get the optimum performance from the batteries, set the regulator to the voltage recommended by the battery manufacturer. For more information, see: http://www.landiss.com/battery.htm http://batteryfaq.org/ As to the original question, I would check the specific gravity of the batteries. Remember that even though your regulator may be set at, say, 28.2, if the batteries are extremely discharged, they may be able to absorb all the current the alternator is capable of. In this case, the voltage will read much lower until the batteries reach a state of charge where the alternator is no longer maxed out, at which point the voltage will steadily rise until it reaches the regulator set point. Also, make certain the regulator sense lead is connected directly to battery positive, and not to the alternator output terminal. -Sean http://OurOdyssey.BlogSpot.com |
John MC9 (John_mc9)
Registered Member Username: John_mc9
Post Number: 1121 Registered: 7-2006 Posted From: 74.162.75.26
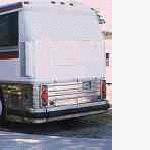
Rating: N/A Votes: 0 (Vote!) | Posted on Friday, April 16, 2010 - 12:23 pm: | |
Matthew - Although my MC9 regulator was best set at 24-1/2 volts for the least amount of water loss, the standard setting is 27-1/2 vdc. I used series 31 batteries and they didn't need water added for less than monthly intervals. You should not expect to add water "at least weekly in daily use", unless your regulator is mis-set and it is causing the batteries to be continually boiled. You can read the actual documentation here: MC9 Documentation. Good luck. |
Sean Welsh (Sean)
Registered Member Username: Sean
Post Number: 1075 Registered: 1-2003 Posted From: 70.134.90.221
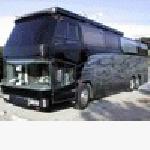
Rating: N/A Votes: 0 (Vote!) | Posted on Friday, April 16, 2010 - 1:35 pm: | |
Note that the recommendation in the MC-9 manual applies for normal use as a bus, where there are no "house systems." So the recommended charge setting, as explicitly stated in the manual, will not fully charge the batteries under normal use. Bear in mind that normal use for a bus involves a very high ratio of run time to engine starts. If you have a dedicated chassis system not interconnected to a house system, that's probably a fine setting. If, however, you have a bridge solenoid or battery isolator and are charging house batteries along with the chassis batteries, you want a higher setting. Remember also that the vehicle manufacturer's goals are different from yours. While a lower setting such as 27.5 will minimize the daily or weekly maintenance required, it will most certainly not optimize the amount of power available from the batteries nor battery life. Battery life, measured either in years or number of cycles, is optimized by vigorous charging, preferably temperature-compensated, coupled with religious attention to electrolyte level and specific gravity. In fact, in a perfect world, you would have the ability to periodically "equalize" the batteries, which is actually a controlled over-charge situation intended to, among other things, energize the electrolyte to the point of bubbling. Most vehicle manufacturers and even many battery manufacturers realize that most users will never pay enough attention to water levels and thus recommend lower, sub-optimal settings basically just to keep people from getting themselves in trouble. Note that a typical 12-volt flooded battery will have a recommended "float" setting of just under 27 volts, and a recommended "bulk" setting of something north of 28 volts as per my previous email. Float settings are intended to keep batteries that are already mostly charged topped up; bulk settings are intended to charge batteries that have been discharged more than 10% or so. MCI is taking a conservative approach by splitting the difference. I stick by my original recommendation. For user-serviceable flooded batteries, best performance is obtained by charging at the battery manufacturer's recommended settings, which will usually result in water needing to be added weekly. (If you drive infrequently and in short bursts, you want the "bulk" setting, if you drive daily for hours and hours you might want to go closer to the "float" setting.) "Maintenance free" flooded batteries, an oxymoron if ever I saw one, should of course be charged at much lower settings because there is no provision to maintain electrolyte levels. I recommend against this type of battery for most applications, although the current price differential between these and traditional models might make the reduced performance and shorter life span a worthwhile tradeoff. What I have always recommended to people who don't want to monitor or maintain water levels on flooded batteries is to spend the extra dollars up front and buy AGMs. You will be money ahead in the long run. -Sean http://OurOdyssey.BlogSpot.com |
les marston (Les_marston)
Registered Member Username: Les_marston
Post Number: 43 Registered: 1-2010 Posted From: 68.151.248.141
Rating: N/A Votes: 0 (Vote!) | Posted on Friday, April 16, 2010 - 3:38 pm: | |
Sean How well do the AGMs stand up to long periods of non use. If I was to use them would a solar panel be necessary for say periods of 4 to 6 months non use? under these conditions would a regular flooded lead acid be better? Les |
Sean Welsh (Sean)
Registered Member Username: Sean
Post Number: 1076 Registered: 1-2003 Posted From: 76.245.98.131
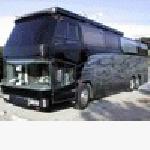
Rating: N/A Votes: 0 (Vote!) | Posted on Friday, April 16, 2010 - 6:26 pm: | |
Actually AGMs have lower self-discharge rates than flooded batteries. That said, usually there are phantom loads on the batteries that tend to drag them down faster. A solar trickle charger is not a bad idea for coaches that sit for long periods. -Sean http://OurOdyssey.BlogSpot.com |
Matthew J Rutkowski (Matt_rutkowski)
Registered Member Username: Matt_rutkowski
Post Number: 6 Registered: 1-2010 Posted From: 98.235.234.208
Rating: N/A Votes: 0 (Vote!) | Posted on Friday, April 16, 2010 - 7:26 pm: | |
Now I have noticed that when I start the coach I have to depress the start button several times before it will turn over I get like a click back near the engine then it will turn over. Could it be a loose starter wire that might not be making full contact? |
Matthew J Rutkowski (Matt_rutkowski)
Registered Member Username: Matt_rutkowski
Post Number: 7 Registered: 1-2010 Posted From: 98.235.234.208
Rating: N/A Votes: 0 (Vote!) | Posted on Friday, April 16, 2010 - 7:28 pm: | |
What I was trying to say could a loose starter wire causee the low voltage problem? |
Paul Lawry (Dreamscape)
Registered Member Username: Dreamscape
Post Number: 650 Registered: 5-2007 Posted From: 64.40.216.39
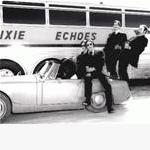
Rating: N/A Votes: 0 (Vote!) | Posted on Friday, April 16, 2010 - 7:44 pm: | |
Any loose wire is a problem. Clean all terminals and make sure they are tight. You need good tight terminals to make that DD spin fast enough to start. Of course topped off batteries help too! Keep the smoke in! |
R.C.Bishop (Chuckllb)
Registered Member Username: Chuckllb
Post Number: 1231 Registered: 7-2006 Posted From: 75.244.32.145
Rating: N/A Votes: 0 (Vote!) | Posted on Friday, April 16, 2010 - 9:57 pm: | |
Matthew... I just went thru that scenario... I have a 100 amp blade fuse that is "before" the starter. However...I also have the house bank wired into the alternator, of course with the start bank. With that in mind, I could not get the "thing" to start as it normally does...one push on the button and it usually is off and going......so, I "serviced" the battery set(s)...even posted a thread here on the matter. Bottom line, after the sets were serviced, re-connected, etc, (double checked for connections in correct order, etc. etc)...guess what...same problem as you are having. Checked the fuse mentioned above and...it was blown. Replaced and ........back to "usual". FWIMBW RCB |
FAST FRED (Fast_fred)
Registered Member Username: Fast_fred
Post Number: 1147 Registered: 10-2006 Posted From: 66.82.9.12
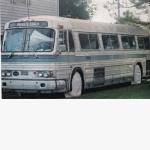
Rating: N/A Votes: 0 (Vote!) | Posted on Saturday, April 17, 2010 - 7:22 am: | |
On many coaches the hassle is always the ground. The spot where the batt set grounds to the frame is always suspect , and can never be clean enough. Remember SS is a lousey conductor of electric , so if you can find them COPPER (not brass)bolts and washers are a big help. FF |
L James Jones Jr (Jamo)
Registered Member Username: Jamo
Post Number: 146 Registered: 11-2007 Posted From: 24.59.114.207
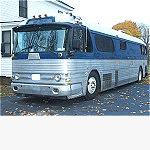
Rating: N/A Votes: 0 (Vote!) | Posted on Saturday, April 17, 2010 - 7:48 am: | |
Matthew, I had that exact problem last year...several hits to the starter switch to get 'er to turn over. I "rebuilt" my solonoid & all is fine. Actually, all I did was remove it, take it apart, clean all contacts, cleaned the copper disc (both sides) & flipped it to the nicer side. Worked for me and took no time at all. Guess I should add to that "no time at all" statement. This operation was performed after spending lots of time cleaning 35' worth of terminals between the bumpers. But...I have an '04 w/6-71. I can sit on a stool at the back bumper & get at the starter/solonoid. Best thing is, you can easily convert a rear bumper to a porto bar. Beers fit nicely... |
Matthew J Rutkowski (Matt_rutkowski)
Registered Member Username: Matt_rutkowski
Post Number: 8 Registered: 1-2010 Posted From: 70.91.44.214
Rating: N/A Votes: 0 (Vote!) | Posted on Saturday, April 17, 2010 - 9:57 am: | |
Could the Starter problem and the charging problem be related?? |
Gary Pasternak (Cessna5354)
Registered Member Username: Cessna5354
Post Number: 82 Registered: 2-2007 Posted From: 71.254.59.159
Rating: N/A Votes: 0 (Vote!) | Posted on Saturday, April 17, 2010 - 10:58 am: | |
The starter & charging problem can very much be related. If my starting batt's are less than 20-21 volts(IIRC) very unlikely I will get a start. The less voltage, the more amps the starter will draw. With loose or corroded connections this will impede the current flow(amps) and your next symptom is the 'click'. Good Luck |
John MC9 (John_mc9)
Registered Member Username: John_mc9
Post Number: 1122 Registered: 7-2006 Posted From: 74.162.81.11
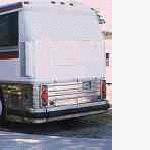
Rating: N/A Votes: 0 (Vote!) | Posted on Saturday, April 17, 2010 - 11:07 am: | |
Re: "Could the Starter problem and the charging problem be related??" Yeah. If it's a ground problem. You asked that originally, remember? ("What do you guys think might be the problem? I am guessing a ground somewhere??") If they did an overhaul and neglected to clean the surfaces that the ground or ground-bond wire(s) are attached to, or if they neglected to tighten a ground or ground-bond connection, you'll have all sorts of problems. Do a close visual inspection at least..... but it'd be better to disconnect each and every ground connection; every ground connection between the engine and frame, batteries and frame, the connections between the batteries...etc... and clean and reconnect each. I did it with mine (when I had it), since the bus didn't appear to have had any serious maintenance for "a long time". Personally, it oughta' be done with any used bus as a precaution, since we don't have the benefit of a company paid tow truck to call. |
Gary Pasternak (Cessna5354)
Registered Member Username: Cessna5354
Post Number: 83 Registered: 2-2007 Posted From: 71.254.59.159
Rating: N/A Votes: 0 (Vote!) | Posted on Saturday, April 17, 2010 - 3:18 pm: | |
To expand my last post, If the batteries are down, there maybe enough current to pull in the solenoid, (The Clicking) but not enough to spin the starter. The starter not spinning may also be the fault of the contacts within the solenoid. These contacts connect the battery 24V to the starter motor windings. Alot of current thru this contact, which is a round disk 1-1/2" dia, This disk makes contact at 3 and 9 o'clock. Leaving 12 and 6 o'clock "unused". Turning this disk 90 degrees will provide "new" contact surface. If you need pic's I think I still have an old solenoid. Hope this makes this clearer, Have a Great Day, |
Donald P H (Eagle19952)
Registered Member Username: Eagle19952
Post Number: 23 Registered: 11-2007 Posted From: 75.223.229.196
Rating: N/A Votes: 0 (Vote!) | Posted on Saturday, April 17, 2010 - 7:30 pm: | |
a lower voltage will increase the amperage across the contact,thus causing the click and the resulting arc which ruins the solenoid....iirc. best to charge properly and do your maintenance,...water vs contact,easy choice for me. |
George M. Todd (George_todd)
Registered Member Username: George_todd
Post Number: 989 Registered: 8-2006 Posted From: 99.68.225.138
Rating: N/A Votes: 0 (Vote!) | Posted on Saturday, April 17, 2010 - 8:55 pm: | |
Having been quite involved with the bus in question, AND having read the original post, lets consider the following. Matt posts "... prior to the overhaul, it was charging 28 Volts..." This bus had a complete re-do of the electric system about 20 years ago. The entire auxiliary drive unit was removed, and all of the auxiliaries are now connected to the gear drives on the back of the engine. It has a totally seperate 12 Volt alternator for the house system. ALL of the diodes in the alt. and the voltage regulator are new, due to a mistake by the prior owner. So, this bus charged immediately before the overhaul, and doesn't charge immediately after, what do we think it might be? Couldn't be an error on the part of the shop could it? Hi Matt, George |
Dallas Farnworth (Dallas)
Registered Member Username: Dallas
Post Number: 40 Registered: 7-2004 Posted From: 72.172.43.196
Rating: N/A Votes: 0 (Vote!) | Posted on Saturday, April 17, 2010 - 9:31 pm: | |
Junction on the pass side cradle rail where the starter, alternator and battery cables meet wasn't replaced correctly? or is loose or broken? |
Matthew J Rutkowski (Matt_rutkowski)
Registered Member Username: Matt_rutkowski
Post Number: 9 Registered: 1-2010 Posted From: 70.91.44.214
Rating: N/A Votes: 0 (Vote!) | Posted on Sunday, April 18, 2010 - 10:36 am: | |
George I totally agree with you I am just trying to avoid taking it back to them to save a little time. They are (the shop) convinced that they didn't forget anything. I however am convinced that they did. Good to hear from you G Dallas I will check that junction today.... thanks for all of the ideas guys |