Author |
Message |
Donald P H (Eagle19952)
Registered Member Username: Eagle19952
Post Number: 30 Registered: 11-2007 Posted From: 75.248.190.159
Rating: N/A Votes: 0 (Vote!) | Posted on Monday, June 28, 2010 - 9:12 pm: | |
Well every time I post here I get good results so I thought I would try again. If there is anything that I dislike about my Coach,this is it. Facts: 1977/8 Eagle 05 8v71n mitre box drives fan (plastic) and alternator. Fan belts two (Gates B86) 89 inch circumfrance 21/32 wide. Problem:I average less 6000 miles per set. Are these the correct belt ? My adjuster/adjustment is a pivotal idler with a stub dowel ON THE BEARING/SHEAVE PLATE that appears to be a/the fulcrum point to utilize a pry bar to accomplish the tension adjustment.Is this the stock/original set-up ? IIRC, THE PIVOT BOLT IS 3/4" and the holding bolt is 5/8" I have tried (in vain) to find EXACT Matched sets. Currently one belt is in the sheave groove (properly),the other is rolled over in the sheave. The longest lasting (current)set was installed using a small bottle jack to adj.the tensioner,(jacking on stub/pivot pry point)...pry bar installed belts have never made 6K miles,even with a cheater pipe....they have slipped and burned up,(lol,i can smell it starting 40 feet away,gives me maybe a mile and a half to get to a safer place so i can put out the triangles and flares...lol) I am wondering if a C86 belt which has a 7/8 top width is the correct belt vs the 21/32 that is there. the cost of replacement is no big deal,but the location of replacement can be a PITA... any thoughts,I don't want a hyd/air clutch fan,I just want to get a real life expectancy from my belts. I have replaced a LOT of belts in my time but these have me stumped. Any thoughts ? PS.I KNOW THAT THERE ARE SEQUENCING NUMBERS ON BELTS,THAT THEY ARE CUT FROM A "PIPE" AND THAT MATCHED SETS ARE NUMERICALLY CORRESPONDING. DOES ANYONE KNOW A DISTRIBUTOR THAT WILL SHIP MATCHED SETS,I think that is my problem....but any thoughts or education or experiance APPRECIATED !!!!. PS hope i have made an understandable post,getting my thoughts on paper isn't my strong suit.... i rode in the small yellow bus :-) |
Ed Brenner (Epbrenner)
Registered Member Username: Epbrenner
Post Number: 43 Registered: 5-2007 Posted From: 174.107.153.15
Rating: N/A Votes: 0 (Vote!) | Posted on Monday, June 28, 2010 - 10:13 pm: | |
I also have a 1977 model 05. My belt number is gates B84 21/32 X 87". Never seen a 05 with plastic blades.I (or dad) never had a belt problem.Are you sure you are not bottoming out adjustment? Your belts are 2" longer than mine I know I would run out of adjustment.All of your bearings in good shape? They don't make matched sets for this belt. I wouldn't want to replace them on the side of the road,always have a set with me so I won't need them. How about alignment between the tensioner pulley and the fan bearing block. did someone replace it when a plastic fan was added? |
George M. Todd (George_todd)
Registered Member Username: George_todd
Post Number: 1054 Registered: 8-2006 Posted From: 99.184.9.29
Rating: N/A Votes: 0 (Vote!) | Posted on Monday, June 28, 2010 - 10:41 pm: | |
I'm quite certain that your problem is mis-alignment! This can be one of two ways, either the two pulleys are not parallel with each other, or they are not the same distance from the rear of the bus. (That's the only way I can think of to describe the second situation.) A straight edge, as in a yardstick, or something slightly longer, is the measuring tool you need. When both pulleys are aligned properly, the straight edge will touch both edges of both pulleys. If you see ANY space between one of the edges, there is the problem. HTH, G |
Buswarrior (Buswarrior)
Registered Member Username: Buswarrior
Post Number: 1880 Registered: 12-2000 Posted From: 174.89.176.29
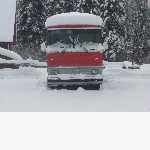
Rating: N/A Votes: 0 (Vote!) | Posted on Monday, June 28, 2010 - 10:51 pm: | |
I'm with George, religiously lay a straight edge against those pulleys, and the tensioner too, all of them flat and in line on front and back edges. I'll summon Jim Shepherd to respond to this post, he used to work for Gates, and has an Eagle. happy coaching! buswarrior (Message edited by buswarrior on June 28, 2010) |
Donald P H (Eagle19952)
Registered Member Username: Eagle19952
Post Number: 31 Registered: 11-2007 Posted From: 75.248.190.159
Rating: N/A Votes: 0 (Vote!) | Posted on Tuesday, June 29, 2010 - 12:01 am: | |
Instant responses,gotta love it.My coach has an oversized radiator. The fan shroud to blade tip clearance is less than 21/32....I just walked out to make sure I wasn't cookoo...it is plastic. The miter box is not adjustabble,the diveshaft has no effect.....the sheave bearing box "ie:approx. 8" round with grease fits is not adjustable,one side drives the alt, inside sheaves drives the fan..)..it is bolted no slots... the super structure angle posts (2" square tube)support member for the adguster seems true...tho perhaps i might could shim it out towards the radiator....the fan "hub" is a pillow block bolted into what appears to be a 1/2" plate.. I just don't see much facility to move the alignment. On my coach with the adjuster pulley slacked off all the way it is a tight squeeze to slip the belts over the pulley edge.I know I am not bottoming out the adj. Does/is my fan drive system stock ??. The coach was maintained by Krause Bus sales in San Antonio,since the day it was new,I am told,and that they did maintenance for Trailways almost from the beginning..... If it is an alighnment problem :-( how would you go about re-alighning....there ain't much room in there...I will check with a straight edge tho... Thanks again :-) I am near Pensacola/FT. Walton,all is well, I got plenty of time,actually parked up in Milton. (Message edited by eagle19952 on June 29, 2010) |
Donald P H (Eagle19952)
Registered Member Username: Eagle19952
Post Number: 32 Registered: 11-2007 Posted From: 75.248.190.159
Rating: N/A Votes: 0 (Vote!) | Posted on Tuesday, June 29, 2010 - 12:35 am: | |
Whoa !!! there are responses over on the Eagle Int board now too. |
Luvrbus (Luvrbus)
Registered Member Username: Luvrbus
Post Number: 908 Registered: 8-2006 Posted From: 74.32.84.228
Rating: N/A Votes: 0 (Vote!) | Posted on Tuesday, June 29, 2010 - 12:44 am: | |
Don, most of the set up is stock the plastic fan is not. I ran the Horton 32 inch 12 blade plastic fan on my Eagle. There is plenty of room to align once you remove the radiator lol |
Donald P H (Eagle19952)
Registered Member Username: Eagle19952
Post Number: 33 Registered: 11-2007 Posted From: 75.248.190.159
Rating: N/A Votes: 0 (Vote!) | Posted on Tuesday, June 29, 2010 - 1:10 am: | |
Don, most of the set up is stock the plastic fan is not. I ran the Horton 32 inch 12 blade plastic fan on my Eagle. There is plenty of room to align once you remove the radiator lol I WAS THINKING THAT PULLING THE ENGINE,TRANS AND THE RADIATOR WOULD MAKE IT WAY MUCH EASIER !!!! |
Donald P H (Eagle19952)
Registered Member Username: Eagle19952
Post Number: 34 Registered: 11-2007 Posted From: 75.248.190.159
Rating: N/A Votes: 0 (Vote!) | Posted on Tuesday, June 29, 2010 - 1:13 am: | |
But seriously what would the collective expertise consider the "tolerance" of true alighnment? .060"....more .125 sounds a bit much maybe... |
Jim Shepherd (Rv_safetyman)
Registered Member Username: Rv_safetyman
Post Number: 307 Registered: 1-2004 Posted From: 72.101.74.64
Rating: N/A Votes: 0 (Vote!) | Posted on Tuesday, June 29, 2010 - 6:36 am: | |
As noted, this subject is on three boards. Here is my post from the BCM board: Ewen, got your email. One of the problems of posting on several boards, is that the other readers do not get to see the replies. Here is the reply I posted on the Eagles International board: The industry adopted a "no match" system many years ago. What this means is that INDUSTRIAL belts (the B86 is an industrial belt) does not have to be ordered as a matched set. The manufacturers tightened their length standards and that allowed the "no match" system to work. Worked well for many years. My guess is that one or more of your pulleys is badly worn, or the drive has somehow become misaligned. It is very hard to check alignment, but you can sight along the strand of the belt to see if there is any kinking. Once a belt has turned over, it will not stay upright. The edge cords will have been damaged on one side. I can't tell if you were saying that you "pried" the belts are. Any significant forcing will damage the belt. If you can't get them on easily, remove one of the pulleys, put the belts in the groove and then install the sheave. I did not check, but many of the "B" sizes have a "BX" equivalent. That belt has notches in the bottom of the belt and premium material. The "B" section belts worked for years and should work on yours if you have properly installed them and checked to makes sure the grooves are not overly worn or that the belts are not misaligned. Would not be a bad idea to check the bearings in the fan stub shaft or the idled to make sure there is not an issue there. Jim (34 years at Gates) |
Jack Campbell (Blue_goose)
Registered Member Username: Blue_goose
Post Number: 146 Registered: 5-2007 Posted From: 71.101.168.79
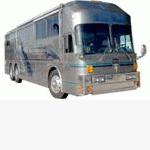
Rating: N/A Votes: 0 (Vote!) | Posted on Tuesday, June 29, 2010 - 7:39 am: | |
My Eagle had the same belt setup as yours for most of the time I have owned the bus. You shouldn't have to tighten the belts more than you can with a bar. If you put too much tension on the belts you will kill the bearings. I ran the set of belts that came on my Eagle for over 100,000 miles. Jack |
Donald P H (Eagle19952)
Registered Member Username: Eagle19952
Post Number: 35 Registered: 11-2007 Posted From: 75.200.225.0
Rating: N/A Votes: 0 (Vote!) | Posted on Tuesday, June 29, 2010 - 12:12 pm: | |
Looks like I have my work ahead of me,RV safetyman over on the Eagle board (and here) has pointed me in the right direction (I think) and that the problem is sheave wear...here is a copy of his advice/speculations,(I THINK on half of one set of sheaves the belts are "bottoming out" and this causes the slipping that ruins the belts...) Jim's post: Concerning alignment, there are two types of alignment. First is where the shafts are parallel and the pulleys are offset. The second is where the shafts are not parallel. Depending on the application, the non-parallel misalignment can be a bit more of a problem. V-belts are pretty forgiving of REASONABLE misalignment. If all of the rest of the drive is good, misalignment of an 1/8" per foot of CD is acceptable on a smooth running drive. That is less than 1* misalignment and some belt drives operate with a misalignment of up to 3 degrees. On an Eagle it is difficult to check alignment. There is not much to get out of alignment. The bearing block is fixed an can only be changed by putting shims in one side. The idler can cause some problems if the pivot for the arm gets worn, but when you draw it up tight with the lock bolt, that should not be an issue. The right angle box is also not prone to getting moved. I don't think you can get a straight edge in the drive area, but you can probably get a string in there. You will need one person to hold it on the fan pulley and then pull it tight and see how the pulleys relate to the tight string. I really lean towards worn pulleys. There are groove gauges that are available at an industrial distributor (such as Motion Industries). You will have to find an old fart that knows what he is doing to get or borrow a set. I have a set I can loan you if you don't find one. However, you can inspect the groove with a straight edge, looking for bowing of the side or look for polishing of the groove in the bottom. The belt should never touch the bottom of the groove. It does not take a lot of pulley wear to begin to cause a problem. Belt turnover is most prevalent on drives with pulsing loads or on drives with high acceleration rates. In the case of our buses, the acceleration rates are not great (race car engines are the type of acceleration that can be a problem). A fan drive should be a smooth load and should not make the belts dance around like they would on a rock crusher or a 1 cylinder pump. Check to make sure you have not lost a blade, or that there would be something to cause a pulsating load. These drives on Eagles were not a problem when the conditions were correct. It appears that someone has modified your fan/radiator system and that suggests that you carefully work you way through all of the things that have been mentioned. Jim |
|