Author |
Message |
joe padberg (Joemc7ab)
Registered Member Username: Joemc7ab
Post Number: 535 Registered: 6-2004 Posted From: 66.38.159.33
Rating: N/A Votes: 0 (Vote!) | Posted on Wednesday, August 10, 2011 - 12:51 pm: | |
I am ready to install new transmission in my MC1 and would like to know the numbers for flywheel to crank and transmission to bellhousing. In all the manuals that I have, I cant find the numbers. Thanks Joe. |
joe padberg (Joemc7ab)
Registered Member Username: Joemc7ab
Post Number: 536 Registered: 6-2004 Posted From: 66.38.159.33
Rating: N/A Votes: 0 (Vote!) | Posted on Wednesday, August 10, 2011 - 2:05 pm: | |
Took a couple of grandkids for a walk to the mailbox, and dawned on me that I had not checked the V71 overhaul manual that I so laboreously Photocopied a few years ago. Section 1.4 page 3 gave the answer, 180-190 ftlbs The other one, Ill go by guess and by golly and use the guide in the 71 manual. |
Brian Evans (Bevans6)
Registered Member Username: Bevans6
Post Number: 62 Registered: 5-2009 Posted From: 67.71.38.163
Rating: N/A Votes: 0 (Vote!) | Posted on Wednesday, August 10, 2011 - 2:40 pm: | |
My manual calls out a specific procedure for flywheel to crank bolts. You use International Compound No 2 or equivalent thread lubricant. I didn't have any so i used an ARP bolt lube. You torque to 50 ft lbs with an accurate torque wrench, then you turn the bolts and additional 90 to 120 degrees. FWIW that is a LOT of torque but I didn't bother to measure what it took to do the additional 120 degrees. The clutch housing bolts are called out at 75 ft lbs, and they should be grade 8 bolts. |
Brian Evans (Bevans6)
Registered Member Username: Bevans6
Post Number: 63 Registered: 5-2009 Posted From: 67.71.38.163
Rating: N/A Votes: 0 (Vote!) | Posted on Wednesday, August 10, 2011 - 2:43 pm: | |
I forgot to say that is for a 8V71 crank and bellhousing. The bellhousing bolts are 7/16" NC thread, and the flywheel bolts are 9/16" NF thread special bolts. |
Jack Fids (Jack_fids)
Registered Member Username: Jack_fids
Post Number: 867 Registered: 1-2009 Posted From: 72.211.145.15
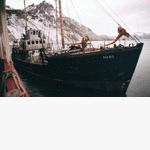
Rating:  Votes: 1 (Vote!) | Posted on Wednesday, August 10, 2011 - 5:07 pm: | |
Way to GO Brian...! today , YOU be Da Man! |
Bill Gerrie (Bill_gerrie)
Registered Member Username: Bill_gerrie
Post Number: 533 Registered: 3-2006 Posted From: 216.198.139.38
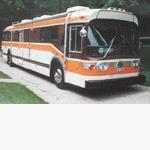
Rating: N/A Votes: 0 (Vote!) | Posted on Wednesday, August 10, 2011 - 5:19 pm: | |
Joe Brian has it right on. They recommend you do not reuse the flywheel bolts. With such a high torque to tighten them they stretch. Not very expensive to replace at a DD dealer. Bill |
Brian Evans (Bevans6)
Registered Member Username: Bevans6
Post Number: 66 Registered: 5-2009 Posted From: 67.71.38.163
Rating:  Votes: 1 (Vote!) | Posted on Wednesday, August 10, 2011 - 7:15 pm: | |
I was thinking further about this, in the context of applying preload to the flywheel bolts. The whole idea of measuring torque when doing up a bolt is to "estimate" the preload you put into the bolt. Preload is the stretch that you get in the fastener, how much you literally stretch it from its static length. When we do up critical bolts in race engines, like rod bolts, we often actually measure the stretch directly with micrometers. In this case we are applying the stretch in a two part process. First we put on a nice slippery lube - the International Compound No. 2 - so that friction between the bolt and the hole is minimized, as well as friction under the head of the bolt. Next we apply a baseline torque just to get things settled down and happy. That 50 ft lbs doesn't stretch a 9/16" bolt at all, it just snugs it up. Now, with slippery threads and no binding we turn the bolt 90 to 120 degrees and what we do is stretch it from pretty tightly snugged up to preloaded. The bolt is 18 threads per inch, one full turn is around 55 thousandths of an inch. 1/4 turn is 13.8 thousandths of an inch, so what we have done is basically stretch the bolt by that amount less some fiddle factor. That preload is carefully calculated to be an amount that creates tremendous rigidity and security in the joint. In an ideal world, you preload the bolt to 75% of it's yield strength. Now for the fun part (I am a hoot at cocktail parties) - the area of that bolt is just under 1/4 square inch. The strength of that bolt is around 125,000 psi. Each bolt, if it's done up to 75% yield strength, is going to apply around 24,000 lbs of clamping force. I think there are 8 bolts, so that is almost 190,000 lbs of force clamping the flywheel to the crankshaft. Fun, eh? Brian |
Jim Shepherd (Rv_safetyman)
Registered Member Username: Rv_safetyman
Post Number: 336 Registered: 1-2004 Posted From: 72.171.0.147
Rating: N/A Votes: 0 (Vote!) | Posted on Wednesday, August 10, 2011 - 7:43 pm: | |
Brian, I love your technical stuff - but then again I am that kind of guy as well When I went to install the flywheel on one of my engines (think the 6V92, but could have been the Series 60) I went to the manual and it said to tighten to 50 ft pounds. I went on one of the boards and confirmed that it should then have the 90* rotation. It turned out my manual did not list the second step!!!! I later found an update to the manual noting the error. Can you imagine the problem if I had just followed the manual? Joe, the big issue will be how you lock the flywheel to keep it from rotating. In my Series 60 manual it talks about a special tapered end bolt that goes into the clutch housing. I took a standard bolt and ground it down to a taper that would fit into the tooth of the flywheel. Worked like a champ. Could not believe that one tooth would hold the flywheel but it did. Jim |
Jim Sanders (Sandy)
Registered Member Username: Sandy
Post Number: 92 Registered: 1-2011 Posted From: 69.199.96.250
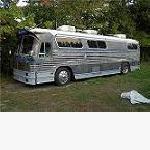
Rating: N/A Votes: 0 (Vote!) | Posted on Wednesday, August 10, 2011 - 7:50 pm: | |
Hey guys any where i can i use grade8 bolts they wont stretch as bad JIM |
Brian Evans (Bevans6)
Registered Member Username: Bevans6
Post Number: 67 Registered: 5-2009 Posted From: 67.71.38.163
Rating: N/A Votes: 0 (Vote!) | Posted on Wednesday, August 10, 2011 - 8:22 pm: | |
Grade 8 bolts won't be strong enough for the flywheel, plus where are you going to get 9/16" bolts? On the clutch housing to bolt the transmission to the engine, grade 8 is fine. I just use a piece of chain to lock the flywheel. bolt one end to the block, one end to the flywheel and tighten away. easy as pie. I've been doing that for years, the same bit of chain that I used to use on Mini engines worked just fine on the 8V71... Brian |
Brian Evans (Bevans6)
Registered Member Username: Bevans6
Post Number: 68 Registered: 5-2009 Posted From: 67.71.38.163
Rating: N/A Votes: 0 (Vote!) | Posted on Wednesday, August 10, 2011 - 8:30 pm: | |
Jim, whats sad is that when I am assembling an engine, for example, which is just an exercise in doing things right and not really thinking, I find myself calculating these things in my head. It takes me a long time to multiply the square of the radius usually, but there I am finding the clamping load of a rod bolt or something when I should be measuring bearing clearances... brian |
joe padberg (Joemc7ab)
Registered Member Username: Joemc7ab
Post Number: 537 Registered: 6-2004 Posted From: 66.38.159.33
Rating: N/A Votes: 0 (Vote!) | Posted on Wednesday, August 10, 2011 - 9:22 pm: | |
Brian Thanks for the boltstretchingggggg lesson. I replaced the rear seal, even though it didnot look that it needed it, just for good measure. I got the flywheel mounted and in place just before supper. I became convinced of using new bolts and scuffplate after seeing what they looked like. The scuff plate was dished like a bowl( somewhat exagerated) and the heads of the bolts are mushroomed. I am using international compound #2. Had to buy a quart can, because it is not sold in small quantity and pricey. My copy of the manual is dated from 1964 and calls for the figures mentioned above. It might be revised in a later edition, if so I would like to know about it. The bellhousing to transmission bolts I torqued to about 80 because of the aluminum housing and the nuts have slots in them to lock them with splitpins Would appreciate a call, number is in the profile Joe. |
Bill Gerrie (Bill_gerrie)
Registered Member Username: Bill_gerrie
Post Number: 534 Registered: 3-2006 Posted From: 216.198.139.38
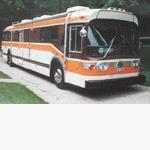
Rating: N/A Votes: 0 (Vote!) | Posted on Thursday, August 11, 2011 - 8:52 am: | |
Joe I hope you used a double lip crankshaft seal. Two different oils in engine and transmission so need to be kept separate. Brian I never really looked at what is going on when you stretch the flywheel bolts but now I see why it is important to replace them each time. Major problems if they came lose. Thanks for the insite to what happens. Bill |
joe padberg (Joemc7ab)
Registered Member Username: Joemc7ab
Post Number: 538 Registered: 6-2004 Posted From: 66.38.159.33
Rating: N/A Votes: 0 (Vote!) | Posted on Thursday, August 11, 2011 - 10:33 am: | |
Bill The seal I installed is identical to the old one,double lip. If it were to leak, any oil would drip out of the bottom of the flywheel housing. Transmission is a sealed box with the clutch inbetween, and specifies engine oil for lubrication. Joe. |
Brian Evans (Bevans6)
Registered Member Username: Bevans6
Post Number: 69 Registered: 5-2009 Posted From: 67.71.38.163
Rating: N/A Votes: 0 (Vote!) | Posted on Thursday, August 11, 2011 - 1:17 pm: | |
My new crankshaft seal came with a new wear sleeve to fit onto the crankshaft. tapped right on easy as pie. Did yours? |
Luvrbus (Luvrbus)
Registered Member Username: Luvrbus
Post Number: 1232 Registered: 8-2006 Posted From: 184.10.191.147
Rating: N/A Votes: 0 (Vote!) | Posted on Thursday, August 11, 2011 - 2:39 pm: | |
All you gain with the new bolts is the factory locktite those bolts don't stretch same with the head bolts DD tells you not use a bunch of bs not one rebuilder I know changes the head bolt on a 2 stroke me I don't use the twist and torque method got my hands on some old DD manuals that show it foot pounds before I had to call on Dallas for the settings he has it ft pounds. Installing and torquing a head with the twist and torque method on a 92 series is almost impossible without another pair of eyes good luck |
joe padberg (Joemc7ab)
Registered Member Username: Joemc7ab
Post Number: 539 Registered: 6-2004 Posted From: 66.38.159.33
Rating: N/A Votes: 0 (Vote!) | Posted on Thursday, August 11, 2011 - 5:48 pm: | |
Clifford Then you are telling me to go with the figure in my manual Brian I got a new wear sleave but didnot have to use it, so it will be returned. |
joe padberg (Joemc7ab)
Registered Member Username: Joemc7ab
Post Number: 540 Registered: 6-2004 Posted From: 66.38.159.33
Rating: N/A Votes: 0 (Vote!) | Posted on Thursday, August 11, 2011 - 7:51 pm: | |
Done!!!! Two hands on my click type torque wrench in stages till the last setting at 185 ftlbs, after chaining the flywheel. Joe. |
larry currier (Larryc)
Registered Member Username: Larryc
Post Number: 365 Registered: 2-2007 Posted From: 207.200.116.13
Rating: N/A Votes: 0 (Vote!) | Posted on Saturday, August 13, 2011 - 1:09 am: | |
If you are roadside, you can use a marker or paint stick and snug + what ever degree they say will get you going fine. Still can build a good running Cat with a cheater pipe Head bolts do wear out, look for narrowing wear directly under the head of the bolt. Thats why they always break the heads off when a head bolt fails. If you passed on the wear sleve, the shaft better be perfect, you are now asking the seal to work at it's max design vrs w/sleve, it might triple its surface coverage with the sleve and the seal is designed to work either way, but it is going to fail sooner without the sleve. |
larry currier (Larryc)
Registered Member Username: Larryc
Post Number: 366 Registered: 2-2007 Posted From: 207.200.116.13
Rating: N/A Votes: 0 (Vote!) | Posted on Saturday, August 13, 2011 - 1:22 am: | |
If you are roadside, you can use a marker or paint stick and snug + what ever degree they say will get you going fine. Still can build a good running Cat with a cheater pipe Head bolts do wear out, look for narrowing wear directly under the head of the bolt. Thats why they always break the heads off when a head bolt fails. If you passed on the wear sleve, the shaft better be perfect, you are now asking the seal to work at it's max design vrs w/sleve, it might triple its surface coverage with the sleve and the seal is designed to work either way, but it is going to fail sooner without the sleve. |
joe padberg (Joemc7ab)
Registered Member Username: Joemc7ab
Post Number: 541 Registered: 6-2004 Posted From: 66.38.159.33
Rating: N/A Votes: 0 (Vote!) | Posted on Saturday, August 13, 2011 - 12:04 pm: | |
Larry I had not made it clear but the shaft allready had a sleeve with basically no wear showing so I took the easier route. Joe. |